|
Bei dem Schweißen von Stahlrohren, Flanschen und Blechen wird zwischen dem Nachlinksschweißen (Linksschweißen < 3 mm Rohrwand-/Blechdicke) und Nachrechtsschweißen (Rechtsschweißen > 3 mm Rohrwand-/Blechdicke) unterschieden. Das Autogenschweißen wird eingesetzt, wenn die Schweißnähte schlecht zugänglich sind, also vor Ort auf der Baustelle und in allen Lagen, unter bestimmten Umständen auch mit einem Spiegel (Linksschweißen). An diesen Stellen ist in der Regel ein Schweißen mit einem E-Schweiß- oder Schutzgashandstück nicht möglich. |
Leider wird des Autogenschweißen in vielen Betrieben nicht
mehr angewendet, weil die Kosten des Schweißens relativ hoch sind, eine erhöhte Gefahrenlage beim Gasschweißen vorhanden ist und auch die heutige Ausbildungspläne im SHK-Handwerk die früher üblichen Schweißkurse nicht mehr vorsehen. Außerdem gibt es immer neue Rohrverbindungstechniken. In der Praxis gibt es Probleme, wenn in den Aufträgen (z. B. Fernheizungen, Rohrleitungsbau) das Autogenschweißen gefordert wird. Hier fehlen oft die Monteure mit den entsprechenden Schweißberechtigungen (gültige Schweißpässe). |
Beim Gasschmelzschweißen (Autogenschweißen oder Acetylenschweißen) wird das Metall mittels offener Flamme, die bei der Verbrennung von Ethin (C2H2 - Acetylen) und Sauerstoff (O2) entsteht, erhitzt und direkt oder durch Zugabe von speziell legiertem Schweißdraht miteinander verbunden. Die Schweißgase werden auch bei dem Brennschneiden eingesetzt. |
|
Autogenschweißgerät
Zu einem Schweißgerät gehören mindestens je eine Acetylen- und Sauerstoffflasche. Auf den Flaschen ist jeweils ein Druckminderventil aufgeschraubt, um den Flaschendruck auf den jeweiligen Arbeitsdruck zu reduzieren. Danach sind Absperrventile und Flammensicherungen (Gebrauchsstellenvorlagen) angeordnet, damit die Flamme nicht in die Flaschen zurückschlagen kann.
Die Schweißflamme wird am Handstück (Griffstück) eingestellt, wobei Acetylen und Sauerstoff im Verhältnis 1:1 bis 1,2:1 gemischt werden. Diese Flamme nennt man neutrale Flamme. Sie kann "hart" oder "weich" eingestellt sein, je nach der Geschwindigkeit, mit der das Gasgemisch aus der Brennermündung strömt. Die Einstellung ist von der Materialdicke abhängig. Die Flamme wirkt bei diesem Mischverhältnis reduzierend, d. h. dass kein Luftsauerstoff mit dem Werkstück eine Verbindung eingehen, und somit eine Oxidschicht bilden kann, die eine gute Verschweißung verhindern würde. Das Acetylen-Sauerstoffgemisch verbrennt in zwei Stufen. In der ersten Stufe findet an der Brennerspitze (Schweißeinsatz, Schweißbrenner) zunächst eine unvollständige Verbrennung statt. Die dadurch entstandenen Gase Kohlenmonoxid und Wasserstoff brauchen zu ihrer restlosen Verbrennung weiteren Sauerstoff, welchen sie aus der umgebenden Luft holen.
Durch die zweistufige Verbrennung wird eine sauerstofffreie Zone um den Flammenkegel gebildet. Diese Zone wird als Schweißzone bezeichnet und wirkt reduzierend. Die reduzierende Zone hat außerdem den Vorteil, dass in ihr, etwa 2 – 4 mm vor dem Flammenkegel, die höchste Temperatur der Flamme liegt (etwa 3200 °C).
In Betrieben, in denen hauptsächlich hartgelötet wird, verwendet man statt Aceztylen aus wirtschaftlichen Gründen Propan in Verbindung mit Sauerstoff. Erfahrene Monteure können auch ohne einen Düsenwechsel damit schweißen und brennschneiden. Zu beachten ist, dass Flüssiggas schwerer als Luft ist, also bei Arbeiten unter Bodengleiche (Keller, Gruben.) nicht eingesetzt werden darf, und die Temperatur der Schweißflamme nur ca. 2.850 °C hat.
Schweißbrenner
(Schweißeinsätze)
Im Schweißbrenner (Schweißeinsatz) werden Sauerstoff und Acetylen im Verhältnis
1:1 bis 1,2:1 gemischt und muss erhalten bleiben. Der Sauerstoffdruck wird mit einem
höheren Druck als das Acetylen zugeführt. Deswegen wird ein Injektorbrenner eingesetzt. Der Sauerstoff
strömt durch die Düse ein. Dabei entsteht hinter der Mischdüse ein Unterdruck, wodurch das einströmende
Acetylen angesaugt und mitgerissen wird. Im Mischrohr vermischen sich die Gase und strömen mit hoher Geschwindigkeit
aus der Schweißdüse aus.
Die Schweißbrenner sind sog. Wechselbrenner, die mit einer Überwurfmutter am Griffstück eingesetzt werden. Hier passt auch auch ein Schneidbrenner. Die Brennergrößen richten sich nach der zuschweißenden Materialdicke (1 > 0,5 - 1 mm, 2 > 1 -2 mm, 3 > 2 - 4 mm, 4 > 4 - 6 mm, 5 > 6 - 9 mm, 6 > 9 - 14 mm). Die Brennergröße und der notwendige Sauerstoffdruck ist auf dem Schweißbrenner eingestempelt. Der Gasverbrauch wird über die
mittlere Materialdicke ermittelt (Materialdicke mal 100 = Gasverbrauch pro Stunde).
Schweißflamme einstellen und anzünden
1. Flaschenventile um höchstens eine halbe Umdrehung öffnen.
2. Arbeitsdruck an den Druckminderer einstellen. Die Einstellschrauben hierbei im Uhrzeigersinn drehen, bis das Arbeitsmanometer den gewünschten Druck (Sauerstoff 1,8 – 2,5 bar, Acetylen 0,2 – 0,8 bar) zeigt.
3. Absperrventile beider Druckminderer öffnen.
4. Schläuche durchspülen und Gasmengen einstellen.
- Sauerstoffabsperrventil am Griffstück um eine Umdrehung öffnen. Sauerstoff einige Sekunden lang ausströmen lassen.
- Dann Ventil schließen, bis nur noch eine geringe Gasströmung vorhanden ist.
- Acetylenabsperrventil am Griffstück um eine Vierteldrehung öffnen. Gasmischung einige Sekunden lang ausströmen lassen.
5. Flamme entzünden.
– Darauf achten, den Schweißbrenner so zu halten, dass niemand gefährdet werden kann.
– Einen Anzünder verwenden.
– Flamme mit den Ventilen am Griffstück justieren.
6. Flamme löschen
- Zuerst das Brenngasventil am Griffstück schließen - dann das Sauerstoffventil. |
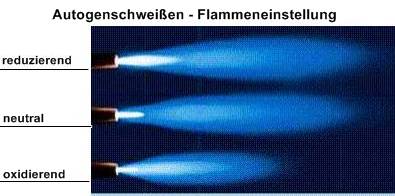 |
Eine leicht reduzierende
Flamme wird für das Schweißen von Messing und Bronze verwendet und kann auch zum
Fugenlöten eingesetzt werden. Die Flamme hat einen leichten Sauerstoffüberschuss.
Eine neutrale Schweißflamme werden für alle Schweißarbeiten an Stahl und Kupfer eingesetzt.Diese Flamme hat einen scharf abgegrenzten Flammenkegel, der kurz vor dem Übergang zum Kohlenstoffkegel erreicht ist.
Eine Acetylenüberschussflamme (leicht aufkohlende Flamme) wird für das Schweißen von Gusseisen,
Aluminium, Blei und Zinklegierungen eingesetzt. Hier wird Acetylen mit soviel Sauerstoff gemischt
wird, dass sich eine deutlich leuchtende gelbe Zone (Aufkohlzone) vor der Kernflamme bildet. |
|
Nachlinksschweißen
(Linksschweißen) kommt bei Stahlrohren bis zu 3 mm
Wanddicke, die in "normalen" Warmwasserheizungen vorhanden sind, zum Einsatz. Die Flamme zeigt in Schweißrichtung,
wodurch das Schmelzbad außerhalb der höchsten Temperaturzone liegt und so klein gehalten werden kann. Die Flamme
schmilzt die Ränder des Materials ab, wobei die Brennerspitze im Kreis oder in Halbkreisen
geführt wird. Der Schweißdraht wird vor der Flamme links geführt und unter dem Flammenkegel
mit tupfenden Bewegungen in das Schmelzbad abgeschmolzen. Die fertige Schweißnaht befindet sich rechts.
Bei Materialdicken über 3 mm ist ein Durchschweißen nicht möglich. Es bildet sich keine Wurzel,
wodurch die Festigkeit der Naht zu gering ist. Hier sollte das Rechtsschweißen eingesetzt
werden. |
|
Nachrechtsschweißen
(Rechtsschweißen) kommt bei Stahlrohren ab 3 mm Wanddicke zum
Einsatz. So sind z. B. Schweißnähte in Nahwärme- und Fernwärmeanlagen und im
Rohrleitungsbau nur durch Rechtsschweißen auszuführen. Die Monteure müssen die Schweißerprüfung nach DIN EN 287 vorweisen können.
Die Flamme zeigt auf die bereits geschweißte Naht, also entgegen der Schweißrichtung und schmilzt die
Materialwandungen bis zur Unterkante ab. Dabei bildet sich eine birnenförmige Öffnung
(Öse). Die Brennerspitze wird nicht hin- und herbewegt, sondern hält nur die Öse offen, ohne die
Schweißnaht zu überhitzen. Die Schweißraupe wird nur durch den Schweißdraht, der mit
kreisender Bewegung im Schmelzbad reibend abgeschmolzen wird, geformt. Das Abschmelzen
der Drahtspitze muss beobachtet werden, damit sich eine gleichmäßige Unterraupe bildet.
Um eine fachgerechte Schweißnaht herstellen zu können, muss die Naht richtig vorbereitet werden.
Hierbei ist auf die richtige Schweißfugendicke (= Schweißdrahtdicke) und saubere Heftstellen zu achten.
Außerdem darf kein Zunder vom Brennschneiden vorhanden sein. |
|
|
|
Flammrichten
Das Flammrichten ist in der Regel die einzige geeignete Methode unerwünschten
Deformationen bzw. Spannungen im Material, die beim Schweißen* und Brennschneiden entstehen und nicht akzeptabel sind, rückgängig zu machen. Das Flammrichten dient nicht nur zum Beseitigen von Verformungen von Schweißkonstruktionen sondern auch zum Richten von Profilen, Schiffbeplankungen oder großflächige Teile aus dünnen Blechen (z. B. Torfüllungen und Kastenkonstruktionen). Das Flammrichten wird auch zur Formgebung eingesetzt.
* Gasschmelzschweißen (Autogenschweißen), Lichtbogenhandschweißen, Metallschutzgasschweißen (MIG / MAG), Wolfram-Inertgasschweißen (WIG) |
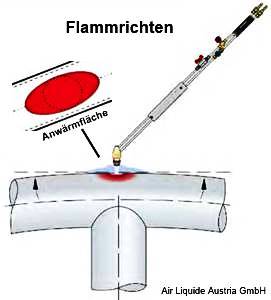
Flammrichten einer Rohrabzweigung
Quelle: Air Liquide Austria GmbH |
|
Besonders groß sind die Verformungen bei Stahlrohren,
die einseitig mit Wärme bearbeitet werden (z. B. Abzweigungen, Schweißmuffen). Die Verformung wird durch ein schnelles lokales
Erwärmen (ca. 600 – 700 °C [Glühfarbe - Dunkelrot]) ohne wesentliche
Gefügeveränderung mit einer Sauerstoff-Acetylen-Flamme und einem speziellen Flammrichtbrenner auf der
Gegenseite und eine Behinderung der Wärmeausdehnung des Materials. Um einen optimalen Wärmestau
zu erzeugen, wird bei Baustählen die Flamme mit hoher Ausströmgeschwindigkeit und Sauerstoffüberschuss (ca. 50%) eingestellt. Dabei
sollte der Abstand Flammenkegelspitze zur Werkstückoberfläche so gering wie möglich gehalten werden. Beim Abkühlen
(an ruhender Luft oder besser mit Wasser) der Anwärmfläche entsteht durch Schrumpfung eine bleibende gewünschte Formveränderung.
Flammrichten - Air Liquide Austria GmbH
Flammrichten - Linde Schweisstechnik GmbH |
|
|
|
|
Brennschneiden
Das Brennschneiden ist ein thermisches Trennenverfahren (autogenes Brennschneiden),
bei dem der Werkstoff (unlegierter und niedriglegierter Stahl) durch eine Brenngas-Sauerstoff-Flamme
(Vorwärmflamme, Heizflamme) örtlich auf die Entzündungstemperatur (ca. 1.150 °C) erwärmt und im reinen Sauerstoffstrahl
verbrennt (oxidiert). Das ausgeblasene Material (Oxide) hinterlässt eine Schnittfuge. Bei diesem Vorgang entsteht Wärme (exotherme
Reaktion). Durch diese Reaktionswärme und durch die von der Heizflamme abgegebene Wärme entsteht eine fortlaufende
Verbrennung (Oxidation).
Bei Stahl erhöht sich mit steigendem Kohlenstoffgehalt die Entzündungstemperatur, aber die Schmelztemperatur nimmt ab.
Bei einem Kohlenstoffgehalt über 1,6 % bis 1,8 % ist die Entzündungstemperatur zum Brennschneiden nicht mehr geeignet.
Legierungsbestandteile (Chrom, Nickel, Wolfram) beeinflussen auch die Brennschneideignung des Stahls, da die Oxide dieser
Bestandteile einen hohen Schmelzpunkt haben. Die Wärmeeinwirkung beim Brennschneiden von Stahl kann im Schnittflächenbereich auch eine Aufhärtung,
Eigenspannungen und Risse verursachen. Die Aufhärtung hängt vom Kohlenstoffgehalt und von der Abkühlgeschwindigkeit ab,
Eigenspannungen werden bei geringer Schneidgeschwindigkeit größer und Risse bilden sich bereits bei Stählen mit mehr
als 0,3 % Kohlenstoff. Durch zusätzliche Wärmeeinbringung mit einem Wärmebrenner während des Brennschneidens und durch Vorwämen kann die Rissgefahr
vermindert werden.
Richtige Flammeinstellung bei Acetylen-Sauerstoff:
Der Schneidsauerstoffstrahl muß gerade und zylindrisch aus der Düse strömen und darf nicht flattern. Die Heizflamme soll den Sauerstoffstrahl
konzentrisch umgeben.
Der Schneidsauerstoffdruck (Stahlrohre > 2,5 - 3 bar [Acetylen > 0,3 bar]) ist von der Materialdicke, dem
Brenner und der Düse abhängig. Die Heizflamme muss neutral (scharf abgegrenzter
Flammenkegel) und weich eingestellt sein, damit es nicht zur Überhitzung kommt.
Wärmzonen der Acetylen-Sauerstoff-Flamme:
Zone 1: Kern und leuchtende Hülle 400 - 600 °C
Zone 2: Schneid- und Schweißbereich 2 bis 5 mm vor der Düse ca. 3.200 °C
Zone 3: Streuflamme rund 2.000 °C |
|
Stahlrohre können mit einem Schneidbrenner von Hand oder
maschinell geschnitten bzw. getrennt werden. Dieses autogene Brennschneiden mit einer Brenngas(Acetylen)-Sauerstoff-Flamme gewährleistet eine hohe Schnittgeschwindigkeit, und ist eines der wirtschaftlichsten Trennverfahren größerer Nennweiten. Bei der richtigen Auswahl der Düsen, Drücke und Schnittgeschwindigkeiten kann ein geschulter Fachmann (Schweißer) die Fertigmaße ohne Nacharbeit herstellen. |
Einige Werkstücke machen es erforderlich, den zu trennenden Bereich vorzuwärmen, da es ansonsten zu Rissen oder einer Aufhärtung im Bereich der Schnittfläche kommen könnte. Grauguss eignet sich jedoch nicht für das Brennschneiden, da der hohe Kohlenstoffanteil eine zu hohe Zündtemperatur hat. Bei anderen Werkstücken, die sich nur bedingt durch Brennscheiden trennen lassen, besteht allerdings die Möglichkeit, auf Sonderverfahren wie z. B. das Metall-Pulver-Brennschneiden zurückzugreifen. |
|
Flammschutzmatte - Hitzeschutz |
Bei vielen Schweiß-, Brennschneid- und Lötarbeiten ist ein passender Hitzeschutz notwendig. Flammschutzmatten, Spritzerschutzdecken und eine Wärmeableitpaste sollten in jedem Kundendienst- bzw. Montagewagen einer Firma, die Schweiß- und Lötarbeiten ausführt, vorhanden sein. Nur mit einem Hitzeschutz ist eine volle Arbeitssicherheit gewährleistet und werden Schäden durch Hitzeeinwirkung vermieden. Eine Rundausrüstung bietet ein Schweißer-Hitzeschutzsicherheitskoffer, der alle Produkte enthält, die bei schwierigen Löt- und Schweißarbeiten Schäden vorbeugen und sauberes und schnelles Arbeiten ermöglichen.
Zur Abdeckung hitzeempfindlicher Teile gibt es viele Flammschutzmatten (bis 3.000°C) und
Spritzerschutzdecken (bis 1.300 °C). Isolierpasten vermeiden die Weiterleitung von Schweiß- und Löthitze. Mit einer solchen
Wärmeableitpaste bzw. Hitzestoppaste können Metalle vor Hitzeeinwirkungen oder Hitzeweiterleitung bis zu 4.000 °C schützen.
Für den Notfall sollte auch immer eine Feuerlöschdecke vorhanden sein.
Hitzeschutz - Linde Schweisstechnik GmbH
Hitzeschutz - Drumm GmbH |
|
Heißarbeit |
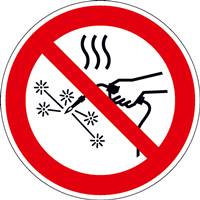
Heißarbeiten verboten
Wenn die Sicherheitsanforderungen nicht eingehalten werden können
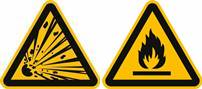
Warnung - explosive und feuergefährliche Stoffe
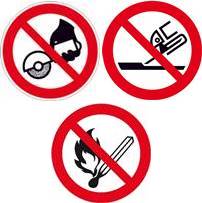
Handschleifen, Seitenschleifen, offene Flamme, Feuer und Rauchen verboten
|
|
Heißarbeiten sind Tätigkeiten (z. B. Schweißen, Schneidarbeiten, Löten, Ausbrennen, Auftauen, Trennschleifen, Arbeiten mit Heißluftgeräten), bei denen ein offenes Feuer, hohe Wärme, ein Lichtbogen eingesetzt werden oder ein Funkenflug entsteht, um Teile miteinander zu verbinden oder zu trennen oder um Hilfsstoffe verarbeitungsfähig zu machen (z. B. Bitumen, Teer). Aber auch Arbeiten mit nicht ex-geschützten Geräten in explosionsgefährdeten Bereichen oder mit funkenerzeugenden Arbeitsmitteln gehören in den Bereich der Heißarbeiten. Auch weitere Arbeitsschritte können je nach Risiko zu den Heißarbeiten gezählt werden. Diese sind dann in der betriebsspezifischen Brandschutzordnung näher festgelegt.
Ein Heißarbeiten-Genehmigungsschein oder Erlaubnisschein wird oft von dem Auftraggeber gefordert, wenn Arbeiten in besonders gefährdeten Bereichen (z. B. Lagerräume, Silos) Heißarbeiten durchgeführt werden. Hier besteht aufgrund der hohen Temperaturen immer eine erhöhte Brandgefahr. Neben den hohen Temperaturen kann unter anderem auch Funkenflug einen Brand verursachen. Besonders gefährlich sind Schwelbrände (z. B. reetgedeckte Häuser, Bauernhöfe, bewohnte Altbauten mit Blindböden [Fehlboden]), weil bei denen erst nach Stunden ein Feuer ausbrechen kann.
Grundlage ist eine allgemein anerkannte Regel der Technik, die besagt, dass vor Aufnahme von Feuer- und Heißarbeiten die ausführende Fachkraft eine Freigabe (Feuererlaubnisschein bzw. Freigabeschein) durch den Auftraggeber oder dessen Beauftragten erhalten muss. |
|
|
Feuer- und Heißarbeiten - WEKA MEDIA GmbH & Co. KG |
Dienstleister benötigen für alle Feuerarbeiten einen schriftlichen Erlaubnisschein
Holcim (Deutschland) GmbH
Sicherheitseinweisung Stufe C für Partnerfirmen und Betriebsfremde
Boehringer Ingelheim Pharma GmbH & Co KG
Wo ist geregelt, dass ein sogenannter Feuererlaubnisschein bei funkenerzeugenden Arbeiten vor Beginn auszufüllen ist?
Landesinstitut für Arbeitsschutz und Arbeitsgestaltung Nordrhein-Westfalen (LIA)
Heißarbeiten-Genehmigungsschein
FM Insurance Europe S.A.
Erlaubnisschein für Feuer- und Heißarbeiten und Arbeiten
mit möglichem Funkenflug
Deutscher Raiffeisenverband e.V.
Erlaubnisschein1
für Schweiß-, Schneid-, Löt-,
Auftau- und Trennschleifarbeiten
Deutsche Gesetzliche Unfallversicherung e.V. (DGUV) |
|
Gefahren beim Gasschweißen |
Beim Gasschweißen und Flammlöten ist die Wärmequelle eine Flamme, die von einem Brenngas-Sauerstoff-Gemisch gespeist werden. Während beim Gasschweißen ausschließlich Acetylen als Brenngas benutzt
wird, kommen beim Flammlöten auch Erdgas, Propan und Wasserstoff zum Einsatz. Brenngas-Luft-Gemische mit Acetylen sind bei 300 °C zündfähig, mit Propan bei 470 °C, mit Wasserstoff bei 560 °C und mit Erdgas bei 590 °C. Eine Explosionsgefahr besteht für Brenngas-Luft-Gemische ab 2 Vol.-% Brenngasanteil. Deshalb darf man Brenngas nie unnötig ausströmen lassen.
Sauerstoff ist selbst nicht brennbar, fördert aber jede Verbrennung erheblich und führt zu einen schneller und intensiver Verbrennung. Außerdem macht es die Flamme heißer und kann Öl und Fett schlagartig zünden. Deshalb darf man Sauerstoff nie zweckentfremden, nie mit Sauerstoff belüften oder kühlen, nie mit Sauerstoff die Kleidung ausblasen, nie Öl und Fett in den Sauerstoffstrom bzw. an die Sauerstoffarmaturen bringen und vorallen nie mit öligen oder fettigen Händen in den Sauerstoffstrom greifen.
Undichtigkeiten führen oft zu einem unbemerkten Austreten von Brenngas oder Sauerstoff. Deshalb muss man stets auf die Dichtigkeit aller Anschlüsse und Verbindungen achten und angeschlossene Brenner dürfen nicht in den Werkzeugkasten gelegt werden. Gasschläuche sind eine Schwachstelle und bedürfen besonderer Aufmerksamkeit. Gasschläuche müssen gegen Abrutschen von den Schlauchtüllen gesichert werden, poröse oder beschädigte Schläuche müssen ausgewechselt werden, die Gasschläuche müssen gegen Überfahren gesichert werden. Allgemein darf nur mit intakten Geräten gearbeitet werden und die Flaschenventile sollten langsam aber zügig geöffnet werden.
Bei Fehlbedienungen des Brenners oder bei Benutzung eines defekten Gerätes kann ein Flammenrückschlag die Folge sein. Mögliche Folgen sind ein Schlauch- oder Flaschenzerknall und Brandverletzungen des Schweißers. Weitere Gefahren drohen durch die optische Strahlung beim Gasschweißen oder Flammlöten im sichtbaren oder infraroten Bereich. Auch ist die Blendwirkung zu beachten. Schutz bieten Schweißerschutzbrillen nach DIN 58112 Verwendungsbereich 6 ober 7 mit Schweißerschutzfilter nach DIN 4647 Schutzstufe 2 - 7 je nach Gasdurchsatz beim Flammlöten oder Schutzstufe 4 - 7 je nach Gasdurchsatz beim Gasschweißen.
Die Lärmentwicklung spielt beim Gasschweißen keine Rolle, da durch einen kleinen Brennereinsatz das Gasschweißen geräuscharm ist. Beim Flammlöten kann der Schallpegel durchaus über 85 dB(A) liegen. Deshalb sollte man entweder lärmarme Mehrlochdüsen verwenden oder Gehörschutz beim Flammlöten tragen.
Sowohl beim Gasschweißen wie beim Flammlöten entstehen bei der Verbrennung Schadstoffe, wobei die wesentlichen Gefährdungen von nitrosen Gasen (= Stickoxide = NOX) ausgeht. Nitrose Gase sind im wesentlichen NO2 (MAK: 5 ml/m3) und NO, N2O4, N2O3 und sind Reizgase mit einem stechenden Geruch, die zu Übelkeit und Kopfschmerzen und sogar zu schweren Lungenschäden führen können. Da beim Flammlöten ein Flußmittel eingesetzt wird, entstehen dort auch Fluor-, Kalium- und Borverbindungen. Bei beiden Verfahren können giftige Rauche beim Verarbeiten von Blei- und Kupferwerkstoffen, verzinkter oder cadmierter Teile oder farb- oder kunststoffbeschichteter Teile entstehen. Dann ist eine zusätzliche örtliche Absaugung notwendig.
Als Vorsichtsmaßnahme sollte man die Flamme nicht unnötig brennen lassen und den Brenner auch in kurzen Pausen zwischen den Arbeitsgängen abschalten. Außerdem ist eine gute allgemeine Raumlüftung notwendig und wegen dem Auftrieb der heißen Gase sollte die Entlüftungsöffnung oben angeordnet sein.
Um hier Unfälle zu vermeiden und die eigenen Augen zu schützen, ist es mehr als ratsam, bei dieser Arbeit eine Schutzbrille zu tragen. Dabei gibt es für die verschiedenen Verwendungsbereiche Brillen mit unterschiedlichen Schweißerschutzfiltern: für die Verwendungsbereiche 6 oder 7 Filter nach DIN 58112, für die Verwendungsbereiche 2 bis 7, bzw. 4 bis 7 - hierbei muss der Gasdurchsatz beim Flammlöten berücksichtigt werden - kommen Brillen mit Filtern nach DIN 4647 zum Einsatz.. |
|
Schweißverfahren, die im Heizungsbau nicht angewendet werden |
• Wolfram-Inert-Gas-Schweißen (WIG): Gleich- oder Wechselstrombetrieb, Lichtbogen zwischen nicht abbrennender Wolframelektrode und dem Werkstoff, Schutzgas: Helium oder Argon, geringe Abschmelzleistung, für dünne Bleche oder Aluminium geeignet.
• Plasmaschweißen: Der Plasmastrahl entsteht durch hocherhitztes, leitendes Gas, Schutzgas: Argon oder Wasserstoff, die starke Energiekonzentration führt zu hoher Schweißgeschwindigkeit, geringer Verzug, Einsatz auch in der Mikroschweißtechnik.
• Metall-Inert-Gas-Schweißen (MIG): Lichtbogen zwischen abschmelzender Drahtelektrode und Werkstück, hohe Abschmelzleistung, tiefer Einbrand, inertes Schutzgas: Argon oder Helium, wird für Aluminium und hochlegierte Stähle verwendet.
• Metall-Aktiv-Gas-Schweißen (MAG): Lichtbogen zwischen abschmelzender Drahtelektrode und Werkstück, hohe Abschmelzleistung, tiefer Einbrand, aktives Schutzgas: Argon mit CO2 oder O2, geringere Schweißgüte als MIG, Einsatz bei niedrig- und unlegierten Stähle.
• Unter-Pulver-Schweißen: Lichtbogen zwischen abschmelzender Drahtelektrode und Werkstück, Abdeckung der Schweißstelle durch Pulver, das durch Schlackenbildung als Schutz der Schmelze dient.
• Elektronenstrahlschweißen: Ein Elektronenstrahl trifft in der Vakuumkammer auf das zu fügende Werkstück, keine Schweißzusätze, kein Schutz gegen Oxidation nötig (Vakuum), hohe Schweißleistungen, verzugsfrei, aber weil sehr teuer auf große Werkstücke beschränkt.
• Laserstrahlschweißen: Ein Rubin- oder CO2-Laser dient als Energiequelle. Einsatzbereiche vor allem in der Mikroschweißtechnik, Feinmechanik sowie immer, wenn mit besonders hoher Präzision geschweißt werden muss.
• Punktschweißen: Schweißen durch Strom in Verbindung mit Presskraft, Übertragung durch zwei Kupferelektroden, Einsatz vorwiegend im Karosserie- und Fahrzeugbau, keine Dichtnähte, Spaltkorrosion.
• Buckelschweißen: Verfahren ähnlich wie das Punktschweißen, zusätzlich aber wird am Werkstück ein "Buckel" zur besseren Übertragung eingeprägt, Platten dienen als Elektroden, geringer Elektrodenverschleiß, durch Schweißroboter können viele Schweißpunkte auf einmal hergestellt werden.
• Rollennahtschweißen: Die Elektroden werden durch zwei sich drehende Kupferrollen geliefert, Schweißpunkte durch Stromimpulse, Dichtnähte bei hohem Impuls möglich, in der Regel noch schneller als Punktschweißen, deshalb große Bedeutung in der Industrie.
• Abbrennstumpfschweißen: Verbinden gleichförmiger, meist runder Querschnitte, Verschweißen der Teile durch wiederholtes Berühren und Trennen der unter Strom stehenden Werkstücke, dabei entstehen Lichtbögen, die das Gefüge auflösen. Anschließend werden die aufgeschmolzenen Enden mit Kraft zusammengepresst. Hohe Festigkeit, auch große Schweißflächen möglich.
• Lichtbogen-Bolzenschweißen (Varianten: Hub- oder Spitzenzündung): Ein Lichtbogen springt zwischen dem Werkstück und dem Bolzen in der Schweißpistole über, das Gefüge beginnt zu schmelzen, anschließend wird der Bolzen in das Werkstück gedrückt und fest verschweißt.
• Ultraschall-Schweißen: Schweißen mittels hochfrequenter, mechanischer Schwingungen (zwischen Amboss und Sonotrode), die die Oxidschichten der Werkstoffe zerstören, relativ geringe Wärmeentwicklung, dünne Schweißzone, immer als Verfahren des Punkt-, Stumpf- oder Rollenschweißens, nur das anstatt Strom und Kraft hier der Ultraschall zu einer Gefügeaufschmelzung und der anschließenden Verschweißung führt. Mittels des Ultraschallschweißens ist ein Verbinden unterschiedlichster Werkstoffe, wie z. B. Glas, Metall oder Kunststoffen, untereinander möglich.
• Reibschweißen: Eines der Werkstücke wird in schnelle Drehung versetzt und gegen das andere, stehende Teil gedrückt. Durch die Reibungswärme schmelzen beide Teile auf, bevor die Drehung gestoppt wird und beide Teile durch große Kraft zusammengedrückt und somit verschweißt werden. Auch mittels des Reibschweißens können unterschiedlichste Werkstoffe (z. B. Stahl mit Aluminium oder Stahl mit Kupfer) dauerhaft und belastungsresistent miteinander verbunden werden.
Quelle:
Fachwissen-Technik - Ute Imkenberg und Thorsten Mauch Datenverarbeitung GbR |
|
Formieren |
Das Formieren ist ein Verfahren, durch das die Nahtwurzel während des Schweißensoder bei dem Hartlöten der Sauerstoff der Innenrohrwandung mit einem Schutzgas bzw. Formiergas ferngehalten wird. Beim Hartlöten von Kupferrohren und Kupferlegierungen (Messing [Kupfer-Zink | Cu-Zn], Rotguss [Rotmessing Kupfer-Zink-Zinn-Legierung | Cu Zn Sn]), und hier besonders bei Kältemittelleitungen, verhindert eine Formierung eine Oxidation (Zunderbildung) der Rohroberfläche an der Innenseite.Lötverbindungen, die unter Verwendung des Formierens entstehen, benötigen keine aufwendigen Nacharbeiten. |
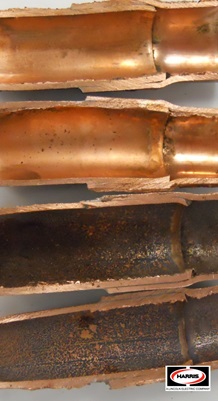
Rohrinnenoberflächen - mit und ohne Formieren
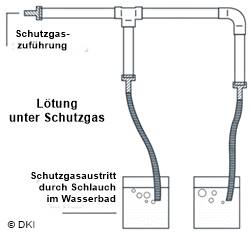
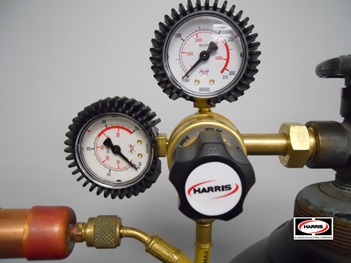
Druckmanometer
Quelle: Harris Products Group |
Ohne das Formieren bildet sich beim Hartlöten bei dem Erwärmen eines Kupferrohres auf der Rohrinnenoberfläche eine helle bis dunkelbraune Verfärbung (Anlauffarben) bis hin zur Zunderbildung. Diese werden dann später, besonders durch HFKW-Kältemittel mit synthetischen Ölen, abgetragen. Die festen Zunderteile können zu Schäden an den Kälte-Armaturen, Ventilen, Mess- und Regeleinheiten führen. Die Folge ist dann ein Anlagenausfall.
Vor und während des Hartlötvorgangs sind die Rohrleitungsabschnitte, in denen Fittings installiert werden sollen, mit trockenen Inertgasen (z. B. Edelgase, Stickstoff und deren Mischungen) oder Formiergas (z. B. Stickstoff-Wasserstoff, Stickstoff-Argon) zu spülen. So bleiben Rohre oxidfrei und es kann eine Oxidation bzw. Zunderbildung auf den Innenoberflächen des Kupferrohres und den Fittings verhindert werden. Hierbei darf der Wasserstoffanteil des Gases aus Sicherheitsgründen einen Maximalwert von 4 Vol.-% nicht überschreiten.
In der Regel wird Stickstoff zum Formieren verwendet. Das Gas wird z. B. durch das Schrader-Ventil in das System eingebracht und auf der anderen Seite durch eine Öffnung über ein Wasserbad abgelassen.
Eine Stickstoff-Gasflasche wird mit einem Druckminderer verbunden und über einen Schlauch oder ein Rohrstück an die Einfüllöffnung der Anlage angeschlossenen. Dabei ist eine Druckeinstellung nicht erforderlich. Es genügt, dass durch das eingebrachte Gasvolumen der Sauerstoff ausreichend verdrängt wird. Dabei hat sich eine Durchflussmenge von 1 - 1,4 l/min oder einem Druck von 0,10 - 0,14 bar bewährt. Das Austrittsventil an der Anlage wird dann soweit geöffnet, bis eine leichte Gas-Ausströmung erreicht ist. Erst dann beginnt man mit dem Erwärmen der Lötstelle und lässt so lange Gas einströmen, bis die Lötstelle erkaltet ist.
Ein zu hoher Gasdruck oder eine zu hohe Durchflussmenge muss vermieden werden, damit die Lötstelle nicht zu stark abkühlt, weil sonst der Lotfluss (die Kapillarwirkung) erheblich beeinträchtigt wird.
.
Kupferrohr gelötet ohne und mit Formieren
Quelle: Messer Group GmbH |
|
Das Formieren in der Schweißtechnik führt nicht nur zu einer verbesserten Qualität der Schweißnähte, sondern kann bei korrekter Ausführung eine Nachbearbeitung der Schweißnähte überflüssig machen.
Die Aufgabe beim Formieren ist erst einmal einfach. Die Luft in einem geschlossenen (oder nahezu geschlossenen) Volumen ist vollständig durch ein Schutzgas zu ersetzen. Aber in der Praxis ist das schwieriger, als man es vermutet. Gase verhalten sich nicht immer wie erwartet, zudem drängt der allgemeine Zeit- und Kostendruck dazu, eine Spülung so schnell wie möglich zu erledigen, was häufig zu nicht optimalen Ergebnissen und vermehrter Nacharbeit führt.
Man unterscheidet drei der Spülungarten:
• Bei einer Verdrängungsspülung schiebt das Schutzgas die zu entfernende Luft bei möglichst geringer Vermischung vor sich her. Dieses Prinzip ist z. B. für große Behälter denkbar. Besonders zu beachten ist hierbei die Dichte des Schutzgases und die Vermeidung von Verwirbelungen. Im Idealfall wird bei dieser Art der Spülung nur so viel Schutzgas verwendet, wie das zu spülende Volumen beträgt, aber dieses Ideal ist in der Praxis nicht zu erreichen.
• Bei der Verdünnungsspülung verteilt sich das Schutzgas gleichmäßig im Raum und vermischt sich mit der zu entfernenden Luft. Die Spülung wird so lange fortgesetzt, bis ein gewisser Restsauerstoffgrenzwert unterschritten wird. Das benötigte Schutzgasvolumen beträgt dabei zwangsläufig ein Vielfaches des Raumvolumens. Die Größe dieses Faktors hängt vom Durchmischungsgrad und vom gewünschten Restsauer- stoffgehalt ab und ist nicht exakt vorhersagbar.
• Die Evakuierungsspülung wird im Bereich der metallverarbeitenden Industrie nur selten eingesetzt. Bei dieser Methode wird das zu spü- lende Volumen zunächst so weit wie möglich evakuiert und dann mit Schutzgas geflutet. Dieser Vorgang kann bei Bedarf mehrere Male wiederholt werden. Zu beachten ist, dass der Behälter dazu vakuumfest sein muss, damit er bei der Evakuierung nicht kollabiert.
Quelle: Dipl.-Ing./EWE Thomas Ammann, Linde AG |
|
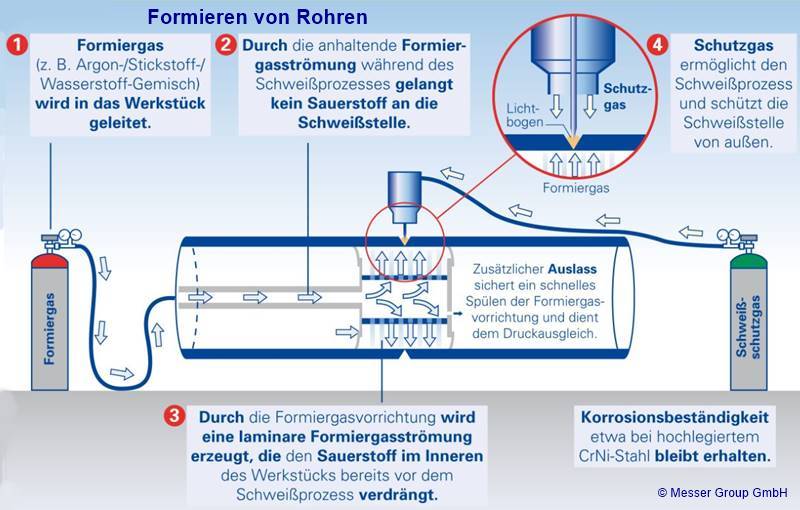
Formieren von Rohren
Formieren beim
Schweißen - Dipl.-Ing./EWE Thomas Ammann - Linde AG
Formieren im Rohrleitungs- und Behälterbau - Messer Group GmbH |
Formieren nichtrostender Stähle - Schweisshelden.de - Linde Schweisstechnik GmbH
Fachinfos zum Formieren von Schweißnähten - Artdefects Media Verlag
|
|
Anlasss- und Glühfarben
Anlassfarben (Anlauffarben) werden durch Interferenz des Lichtes verursacht und Glühfarben werden durch Wärme erzeugt. An den Anlassfarben und Glühfarben des Metalls erkennt man die Arbeitstemperatur bei der Erwärmung.
Eine mögliche Methode für das Anlassen besteht im Erhitzen des Werkstücks unter Einwirkung von Luftsauerstoff. Dies kann mit einer Gasflamme, auf einer beheizten Platte, in einem Muffelofen oder in einem Sandbad erfolgen. Verläuft der Temperaturanstieg über das gesamte Werkstück gleichmässig, entsteht eine homogene Färbung.
Der beim Anlassen erzielte Farbton ergibt sich einerseits aus der Dicke der Oxidschicht, die in Abhängigkeit von Dauer und Höhe der Temperatureinwirkung variiert. Zusätzlich beeinflusst die Art des Metalls oder der Metalllegierung entscheidend, welche Anlauffarbe bei welcher Temperatur zum Vorschein kommt.
Glühfarben werden beim Glühen eines Metalls bei hohen Temperaturen beobachten. Diese Farben entstehen nur, wenn die Wärme wirkt, nach dem Abkühlen sind sie nicht mehr vorhanden. Physikalisch gesehen stellen die Glühfarben thermische Strahlung dar. Das Strahlungsverhalten heißer Metalle entspricht annähernd dem eines schwarzen Körpers. Im Idealfall hängt das Spektrum dieser Strahlung ausschließlich von der Temperatur des Körpers ab. Welche Intensität diese Strahlung besitzt und wie deren Wellenlänge verteilt ist, beschreibt das Planck’sche Strahlungsgesetz. Nach diesem Gesetz verschiebt sich die von einem erhitzten Körper emittierte Strahlung mit steigender Temperatur immer mehr in den kurzwelligen Bereich. Quelle: Frau Dr. Bozena Arnold - MaterialMagazin
Auf Kupfer entwickelt sich mit steigender Temperatur eine Anlassfarbenreihe von Orange über Rosenrot, Violett, Stahlweiss, Messinggelb, Fleischrot bis Grün mit vielen Zwischentönen. |
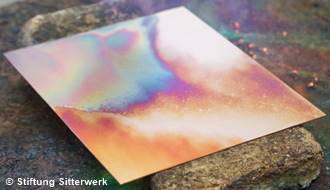
Anlassfarben des Kupferblechs von Orange über Rosenrot, Violett, Stahlweiss, Messinggelb, Fleischrot bis Grün
|
.
|
|
Bei Stahl erstreckt sich das Anlassfarbenspektrum von Weissgelb über Weißgelb, Rot, Violett, Kornblumenblau bis Grau. |
|
|
Glüh- und Anlassfarben - Frau Dr. Bozena Arnold, MaterialMagazin |
Praktische Anwendung
Die Glüh- und Anlassfarben werden z. B. bei Schmiedearbeiten benötigt. Die Schmiedbarkeit ist nur innerhalb eines bestimmten Temperaturbereichs gegeben. Beim Stahl hängt dies neben dem Kohlenstoffanteil auch von den anderen Legierungsbestandteilen ab.
Wenn der kohlenstoffhaltiger Stahl >0,3 % abgeschreckt (Öl oder Wasserbad, teilweise Luft) wird, dann ist er extrem hart, aber sehr spröde. Durch ein nochmaliges Erwärmen wird der Stahl wieder elastischer, verliert aber auch an Härte. Der Stahl ist trotzdem immer noch hart genug. Die Anlasstemperaturen bewegen sich zwischen 200 und 360 °C. Dabei wird der Stahl um so weicher, je höher die Temperatur ist. |
Abhängig von der Umformtemperatur unterscheidet man:
- Warmumformung beim Schmieden von Stahl:
Arbeitstemperatur liegt oberhalb der Rekristallisationstemperatur, zwischen 950 und 1250 °C
Große Umformbarkeit der Werkstoffe, geringe Umformkräfte
- Halbwarmumformung beim Schmieden von Stahl:
Arbeitstemperatur liegt für Stahl bei 750–950 °C
Kein bzw. geringes Verzundern an der Oberfläche, geringere Umformkräfte als beim Kaltumformen
- Kaltumformung (Kaltumformung ist im engeren Sinn kein Schmieden) von Stahl:
Arbeitstemperatur liegt bei Raumtemperatur, eigene Erwärmung auf bis zu 150 °C durch die Umformenergie, enge Maßtoleranzen sind erreichbar.
Keine Verzunderung der Oberfläche, Erhöhung der Festigkeit und Verringerung der Dehnung durch Kaltverfestigung
- Thixoschmieden:
Arbeitstemperatur liegt zwischen Solidus- und Liquidustemperatur der jeweiligen Stahllegierung und damit deutlich über der Warmschmiedetemperatur, Umformbarkeit ähnlich dem Gießen, geringe Umformkräfte
|
Schmiedetemperatur - Verein Alte Schmiede Mambach e.V. - Zell im Wiesental |
|
|
|
Hinweis! Schutzrechtsverletzung: Falls Sie meinen, dass von meiner Website aus Ihre Schutzrechte verletzt werden, bitte ich Sie, zur Vermeidung eines unnötigen Rechtsstreites, mich umgehend bereits im Vorfeld zu kontaktieren, damit zügig Abhilfe geschaffen werden kann. Bitte nehmen Sie zur Kenntnis: Das zeitauf-wändigere Einschalten eines Anwaltes zur Erstellung einer für den Diensteanbieter kostenpflichtigen Abmahnung entspricht nicht dessen wirklichen oder mutmaßlichen Willen. Die Kostennote einer anwaltlichen Abmah-nung ohne vorhergehende Kontaktaufnahme mit mir wird daher im Sinne der Schadensminderungspflicht als unbegründet zurückgewiesen. |