Korrosion
(corrodere > zerstören, zerfressen, zernagen) und Korrosionsschutz
sind Themen, die in vielen Bereichen in der Metallverarbeitung
(Industrie und Handwerk), aber auch bei Betonbauwerken
und zementausgekleideten Rohrleitungen und Bauteilen
(Abwasserleitungen) von großer Bedeutung sind und enorme Schäden
verursachen. Die Erscheinungsformen der Korrosion sind
vielfältig und setzen ein umfangreiches Fachwissen
voraus, um Korrosion zu vermeiden oder
Korrosionsschäden zu beseitigen.
|
Die Grundlagen der Korrosionsvorgänge
beruhen in der Hauptsache auf |
-
chemischen Vorgängen
- elektrochemischen Vorgängen
-
- metallphysikalischen Vorgängen
(z.B. "Zinnpest" > Zerfall des Zinns (z. B. Weichlot) bei
sehr tiefer Temperatur durch Gitterumwandlung)
-
|
Unter Korrosion
versteht man den Angriff und die Zerstörung
metallischer Werkstoffe durch Reaktionen mit Wirkstoffen
aus der Umgebung. Die entstehenden Korrosionsprodukte
(z.B. Rost [FeO(OH) Eisenoxidhydroxid] bei Stahl / Natriumcarbonatocuprat(Il)-Trihydrat
bei Kupfer / Al(OH)3 bei Aluminium) können löslich,
unlöslich aber auch festhaftend
sein. Durch die Korrosion wird die Oberfläche eines Metalls verletzt
bis hin zum totalen Materialabbau. Außerdem werden z. B. die Querschnitte
von Rohrleitungen durch die großvolumigen Korrosionsprodukte
verengt bis hin zum totalen Dichtsetzen. |
|
|
Die
Erscheinungsformen der Korrosion
nach Art des Abtrages
und mechanischer Belastung sind: |
- Eine Kontaktkorrosion
bildet sich durch ein galvanisches Element an der
Kontaktstelle verschiedener Metalle.
- Eine Erosionskorrosion
(Kavitationskorrosion [punktuelle
bzw. kleinflächige Abtragungen]) entsteht durch
Kavitation
und Implosionen an Engstellen (z.
B. Rohrbögen, unentgratete Rohre, eingedrücke
verengte Rohrquerschnitte) oder in Armaturen und Pumpen
in Verbindung mit hohen Fließgeschwindigkeiten
von Flüssigkeiten. Eine Erosion
kann auch durch feste Stoffe (z.
B. Sand) infolge eines Abriebes hervorgerufen
werden.
- Eine selektive
Korrosion (interkristalline/transkristalline
Korrosion) entsteht an den Korngrenzen in ferritischen
Cr- und austenitischen CrNi-Stählen (Edelstahl).
Dabei kann das Gefüge so stark geschwächt
werden, dass ein Kornzerfall eintritt.
Bei einer Temperaturerhöhung auf 400 bis 800
°C scheiden Chromcarbide an den Korngrenzen des
Metallgefüges aus. Durch Auswaschungen in säurehaltigen
Flüssigkeiten reduziert sich anschließend
der zur Passivierung erforderliche Chromanteil in
der Legierung.
- Eine abtragende
Korrosion (Rosten - gleichmäßiger
Flächenabtrag, ebenmäßige Korrosion)
entsteht durch Wasser und/oder verunreinigte Luft,
dabei wird Metall parallel zur Oberfläche abgetragen.
- Eine Lochfraßkorrosion
(Pitting) entsteht durch eine punktuelle Verletzung
einer Schutzschicht an der Materialwandung (Poren
in Überzügen oder durch Chloridangriff auf
Passivschichten). Es entstehen punktuelle, kraterförmigen
oder nadelstichartigen Vertiefungen.
- Eine Spaltkorrosion
bildet sich zwischen Konstruktionsteilchen oder in
Spalten im Metall, da ein Elektrolyt durch Kapillarwirkung
festgehalten wird. Durch große Potentialunterschiede
zwischen den verschiedenen Metallen entsteht eine
elektrochemische Spannungsreihe.
- Eine Spannungsrisskorrosion
(SPRK) tritt nur dann auf, wenn ein Werkstück
oder Bauteil Zugspannungen enthält,
der verwendete Werkstoff eine SPRK-Empfindlichkeit
besitzt und ein spezielles Medium einwirkt. Es entsteht
eine Rissbildung unter mechanischer Beanspruchung
in Anwesenheit von korrosionsbildenden Flüssigkeiten
(z. B. chloridhaltig und stark alkalisch) bei austenitischen
CrNi-Stählen (Edelstahl).
- Eine
Schwingungsrisskorrosion
(SwRK) kann
bei jedem metallische
Werkstoff in jedem
Elektrolyten vorkommen. Die Brüche
entstehen ausschließlich durch transkristalline
Risse, die senkrecht zu den wirkenden Hauptnormalspannungen
entstehen.
- Eine
Filiformkorrosion (fadenförmige
Korrosion) tritt bei beschichteten Metallen und Legierungen
(Stahl und Al-Legierungen) auf. Die Korrosion entsteht
durch eine hohe relative Luftfeuchte
(60 bis 95 %), Verunreinigungen der Oberfläche,
ausreichende Durchlässigkeit der Beschichtung
für Wasser und Sauerstoff, Startersalze (z.B.
NaCl, Chloride [Tausalze], salzhaltige Meeresluft)
und mechanische Beschädigungen der Beschichtung.
In den Küstengebieten im westlichen Europa gibt
es besonders bei Al-Legierungen im Bauwesen (Fassadenverkleidung)
Probleme.
- Eine Schwitzwasserkorrosion
entsteht durch Staub oder Fremdrost am niedrig- und
unlegierten Stahl, sowie an nichtrostendem CrNi-Stahl
(Edelstahl). Dabei wird die Oberfläche stark
angegriffen.
- Eine Taupunktkorrosion
(Säurekondensatkorrosion) entsteht
bei einer Taupunktunterschreitung, wobei Wasser oder
Säure (z. B. aus Verbrennungsgasen im Kessel
oder Abgasrohr) auf Metalloberflächen kondensieren
und zu örtlichen oder flächenhaften Schäden
(gleichmäßige Flächenkorrosion
und Muldenkorrosion) führen.
- Eine Stillstandskorrosion
(Sauerstoffkorrosion)
entsteht an unlegierte Stählen
in Anlagen oder Anlagenteilen, die längere Zeit
ruhendenden Flüssigkeiten ausgesetzt sind. Hier
bilden sich in sauerstoffreichen wäßrigen
Medien nichtschützende, voluminöse Korrosionsprodukte.
Eine zunehmende Konzentration kann ein Aufschaukeln
der Korrosionsgeschwindigkeit bewirken.
- Eine
mikrobiologisch induzierte Korrosion
(MIC) entsteht in Anlagen,
die häufig stagnierendes oder
langsam fließendes Wasser haben.
Dabei kann das Wasser auch biozidfrei
sein, weil sich Mikroorganismen,
die an den vom Wasser berührten Rohrwandungen
haften, bei niedrigen Temperaturen wachsen und vermehren.
Einzelne Ansiedlungen bilden einen primären Film
bis hin zu einem makroskopischen Bewuchs. Diese Vorgänge
sind auch als "Biofouling"
bzw. auch unter den Begriff "Biokorrosion".bekannt.
|
|
|
|
|
|
|
|
|
Eine
Kontaktkorrosion bildet sich durch
ein galvanisches Element an der Kontaktstelle verschiedener Metalle und
ist abhängig von |
- Elektrolytzusammensetzung
- Elektrolytwiderstand
- Potenzialdifferenz
- Flächenverhältnis des edleren zum unedleren
Metall
|
|
Kontaktkorrosion
nennt man auch eine beschleunigte Korrosion
eines metallischen Bereichs, dabei besteht
das Korrosionselement aus einer Paarung aus Metall/Metall
oder Metall/elektronenleitender Festkörper.
Hierbei ist der beschleunigtkorrodierende Bereich die
Anode des Korrosionselements.
Diese Korrosionsart tritt häufig in Mischinstallationen
(z. B. Kupfer/Stahl) oder bei Mischbauteilen,
(z. B. Leichtmetall mit Stahlelementen oder bei oberflächenbeschichteten
Bauteilen) auf.
Der Ionenstrom kann von allen Elektrolyten
(leitenden Flüssigkeiten) übernommen werden
(z. B. Trinkwasser oder Kondenswasser). Die Elektronenleitung
erfolgt an den Kontaktstellen der Festkörper
(z. B. Verschraubung, Schraubenkopf und verspannte Teile).
In vielen Fällen reicht schon die Feuchtigkeit aus
der Luft zum Entstehen einer Kontaktkorrosion.
Das Stärke der Korrosion hängt
immer von der Potentialdifferenz, dem
Flächenverhältnis der miteinander
gepaarten Metalle oder Bauteile
und der Leitfähigkeit der sie bedeckenden
Elektrolyten ab.
|
Eine andere
Art der Kontaktkorrosion ist eine
Lokalelementbildung |
- zwischen
verschiedenartigen Legierungsbestandteilen an der
Metalloberfläche
- zwischen Fremdmetallteilchen,
die in Rohrleitungsteilen eingeschwemmt oder in Oberflächen
eingepresst wurden
- bei einer Entstehung
von anodischen und kathodischen
Bereichen, die sich durch Gegensätze im metallischen
Werkstoff (z. B. an kaltverformten Stellen unterschiedlicher
Umformgrade [z. B. Schrauben mit halben Gewinde]). |
Eine Kontaktkorrosion
kann besonders bei gelöteten Plattenwärmeaustauschern
(Trinkwassererwärmer - Frischwasserstation) aus nichtrostendem
Stahl auftreten. Bei dem Kontakt mit dem edleren
nichtrostenden Stahl kann es zu einer Auflösung
des Kupferlots kommen. Hierbei kann es
zur Außenseite oder zur Seite des Primär-Heizmediums
undicht werden. Auch in Warmwasserleitungen
aus feuerverzinktem Stahl sind schwere
Schäden durch Lochkorrosion möglich,
die durch die bei der Korrosion des Kupferlotes
in Lösung gehenden Kupfer-Ionen verursacht werden.
|
|
|
|
|
|
|
|
|
|
Spaltkorrosion
in einer Pressverbindung bei Edelstahlrohren |
Quelle:
TU Wien |
|
Eine
Spaltkorrosion bildet sich zwischen
Konstruktionsteilchen oder in Spalten bzw. Rissen im Metall,
in denen ein Elektrolyt durch eine Kapillarwirkung festgehalten
wird. Durch große Potentialunterschiede
zwischen den verschiedenen Metallen entsteht eine elektrochemische
Spannungsreihe. |
In Spalten
(Beschädigungen von Oberflächen) und Toträumen
(z. B. in Pressverbindungen) bei metallischen Werkstoffen
(Rohrleitungen, Verbindungen), die oxidische Schutzschichten
bilden, reagiert die Flüssigkeit mit der Werkstoffoberfläche
und verringert den Sauerstoffanteil. Hier hydrolysieren
die entstehenden Korrosionsprodukte, der
pH-Wert fällt und Anionen
wie Chlorid-Ionen können einwandern.
Dadurch kann die oxidische Schutzschicht nicht mehr aufrecht
erhalten werden und es kommt im Spalt zu einer starken Korrosion.
In diesem Spalt entsteht aufgrund des sehr geringen
Volumens schnell ein aggressive Flüssigkeit. |
Weitere Stellen,
an denen sich eine Spaltkorrosion bildet, sind die Gewindegänge
von Schraubverbindungen, Zwischenräume an Dichtungen
und zwischen Wellen und Schutzhülsen. |
Aber auch bei Werkstoffen,
die äußerst empfindlich auf Flußsäure
und Fluoride reagieren, kann nach längerer Betriebszeit
unter PTFE-haltigen Flachdichtungen leichte Aufrauhungen
entstehen. |
|
|
|
Eine
Lochfraßkorrosion (Pitting) entsteht
durch eine punktuelle Verletzung einer Schutzschicht
an der Materialwandung (Poren in Überzügen oder durch Chloridangriff
auf Passivschichten). Es entstehen punktuelle, kraterförmigen
oder nadelstichartigen Vertiefungen. |
|
Lochfraß-
und Muldenkorrosion |
|
Bei der Lochfraßkorrosion
findet der elektrolytische Metallabtrag nur
an kleinen Bereichen (lokalbegrenzt) an der
Rohrwandung statt. Die entstehenden Löcher
sind in der Regel scharf begrenzt und die
Umgebung ist nicht oder nur schwach angegriffen. Da neben
den Löchern noch die volle Wanddicke vorhanden ist, sieht
es wie mit einem Bohrer hergestelltes Loch aus. Der Materialabtrag
kann sehr schnell stattfinden. Neben der
Lochfraßkorrosion findet in den meisten Fällen
auch eine langsam fortschreitende Muldenkorrosion
statt. |
Das Entstehen von Belüftungselementen
(Evans-Element) ist die Grundlage für eine Lochfraßkorrosion
an unlegiertem und niedriglegiertem
Stahl. |
Wenn ein Konzentrationsgefälle
von Sauerstoff vorhanden ist, dann geht das
Eisen an schlecht oder nicht belüfteten Stellen (Lokalanode)
in Lösung. An der Lokalanode wird die Elektrolytlösung
sauer, da eine Hydrolyse der Korrosionsprodukte
des Eisens stattfindet. An gut belüfteten Stellen (Lokalkathode)
wird Sauerstoff zu Hydroxyl-Ionen reduziert und die Elektrolytlösung
alkalisch. Durch die Alkalisierung
kann zu einer spontanen Passivierung des
Stahles kommen und durch die Ausscheidung
von Korrosionsprodukten (Eisen(III)-Hydroxid),
durch die ebenfalls Deckschichten gebildet werden, wird die
Korrosion an der Lokalkathode verhindert. Außerdem wirken
lokal unterschiedliche pH-Werte mit dem unterschiedlichen
Sauerstoffgehalt noch verstärkend auf den Korrosionsfortschritt. |
|
|
Ein Kupferrohr kann nicht "rosten", aber es kann zu Lochfraß kommen. Sauerstoffarmes, saures und hartes Wasser mit einem pH-Wert unter 6 begünstigt die Entstehung von Lochfraß. Andererseits fördert sauerstoffreiches, weiches Wasser mit pH-Werten über 6 das Bilden einer eigenständigen Schutzschicht (Kupferoxid) auf der Innenseite des Kupferrohres. Daraus ergibt sich dann in Zusammenhang mit Kohlensäure ein Salz (Kupferkarbonat). Zusammen mit noch weiteren Salzen (z. B. Chloride, Sulfate) entsteht die braungrüne Patina als passiver Schutzbelag. Wenn dagegen Essigsäure und Kupfer chemisch das Kupferazetat bilden, entsteht Grünspan. Das Ergebnis dieser chemischen Reaktion führt bei weiterer Ausbreitung zu Lochfraß im Kupferrohr.
Aber auch nicht oder schlecht entgratete Kupferrohre, minderwertige Rohrqualität, unsachgemäße Bearbeitung oder Verunreinigungen durch Metallteilchen können Ursachen für den Lochfraß im Kupferrohr sein. Dieser äußert sich anfangs durch ganz feine Löcher, die sich nach innen weiter fressen, vergrößern und zu irreparablen Schäden führen können. Vor allem, wenn viel warmes oder heißes Wasser fließt, entsteht im Kupferrohr leicht Lochfraß. Auch an Leitungsenden bzw. an den Zapfstellen, wo der Sauerstoffgehalt besonders niedrig ist, besteht Gefahr durch Lochfraß.
Wenn Kondensatwasserleitungen bei Brennwert-Gasthermen und Öl-Brennwertkessel mit Kupferrohr ausgeführt werden, dann ist eine Korrosion vorprogrammiert. Deswegen ist Kupfer für diese Leitungen unzulässig (DIN 1986 Teil 4).
.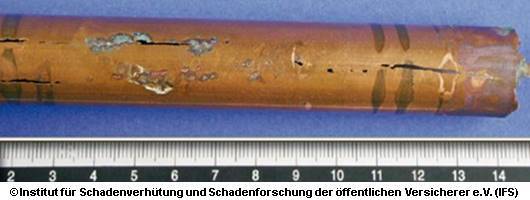
Schäden durch Kondenswasser |
Kondenswasser zerstört Kupferleitung
Institut für Schadenverhütung und Schadenforschung der öffentlichen Versicherer e.V. (IFS)
Korrosion Kupferleitungen - MERUS GmbH
Lochfraß in Kupferrohren reparieren - e-Max-Haustechnik - TradeCom GmbH |
|
Eine
selektive Korrosion (interkristalline/transkristalline
Korrosion) entsteht an den Korngrenzen in ferritischen Cr- und
austenitischen CrNi-Stählen (Edelstahl). Dabei kann das Gefüge
so stark geschwächt werden, dass ein Kornzerfall
eintritt. Bei einer Temperaturerhöhung auf 400 bis 800 °C scheiden
Chromcarbide an den Korngrenzen des Metallgefüges aus. Durch Auswaschungen
in säurehaltigen Flüssigkeiten reduziert sich anschließend
der zur Passivierung erforderliche Chromanteil in der Legierung. |
Kristallite
in einem Legierungsgefüge (z. B. Kupfer- und Zink-Kristallite
in Messing) reagieren an der Oberfläche über einen Wasserfilm
miteinander, weil sie aus Verbindungen mit unterschiedlichem elektrochemischen
Potential bestehen. Der Korrosionsangriff entsteht bevorzugt
entlang bestimmter Gefügebereiche des Werkstoffs. |
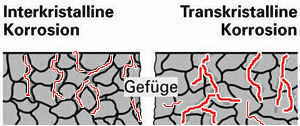 |
Nach dem Bereich
des zerstörten Gefüges unterscheidet
man:
- Interkristalline Korrosion Die Zerstörung
verläuft entlang der Korngrenzen (nichtrostenden Chrom-
und Chrom-Nickel-Stahl, Nickel-, Kupfer-, Zink- und Zinnlegierungen).
Dabei werden Legierungsbestandteile ausgeschieden.
- Transkristalline Korrosion Die Zerstörung
(elektrische Spannungsunterschiede und starke Zugbeanspruchung)
verläuft durch die Gefügekörner. Diese Korrosionsart
wird auch unter "Spannungsrisskorrosion"
eingeordnet. |
|
|
Der Fortschritt
dieser Korrosion kann nur unter der Lupe erkannt werden,
da die selektive
Korrosion im Korngrößenbereich auftritt.
Auf der Korrosionsschicht sind dann Absätze erkennbar. |
Die
Messerlinienkorrosion ist eine Sonderform
der interkristallinen Korrosion, die nach dem Schweißen
von Edelstahl (stabilisierter Kohlenstoffstahl - 12 %
Chrom) auf beiden Seiten der Schweißnaht auftreten kann. Die Gründe
liegen in der Auflösung der Niobcarbide
bei den hohen Temperaturen und der Ausscheidung von
Chromcarbiden nach einer anschließenden Wärmebehandlung
(Temperaturbereich von ca. 600 °C). An der Schmelzlinie bildet
sich eine schmale, messerlinienfeine, selektiv angegriffene
Zone, was auf eine Anreicherung von
Carbiden zurückzuführen ist. Dadurch wird in
diesem Bereich der Chromgehalt von 12 % unterschritten
und es bildet sich keine Schutzschicht aus Chromoxid,
die das Material vor einer weiteren Korrosion schützen soll. |
Bei
der Messerschnittkorrosion handelt es sich um eine
Grenzflächenkorrosion. Diese tritt bei hartgelöteten
Edelstahl-Bauteilen (z. B. Wärmetauscher) auf,
die z.B. bei mit zinkhaltigen Loten hergestellt werden.
Ausschlaggebend ist der Kontakt mit chloridhaltigen,
wässrigen Medien.
Hier wird die Stahloberfläche am Rand
und unter der Lötstelle angegriffen.
Die Korrosionsgefahr wird durch Löten mit Zn-freien
Loten und Flussmittel verringert. Bei Ofenlötungen (ohne Flussmittel),
z.B. mit Kupferlot, gibt es keine Messerschnittkorrosionsfälle.
Am sichersten sind Lötverbindungen mit Ni-Basislot.
Korrosionsschäden
an gelöteten Plattenwärmetauschern - G. Pajonk
/ Materialprüfungsamt NRW |
|
Außen- und Innenkorrosion mit Rost- und Magnetitschlamm |
Eine
abtragende Korrosion (Rosten
- gleichmäßiger Flächenabtrag, ebenmäßige
Korrosion) entsteht durch Wasser und/oder verunreinigte
Luft, dabei wird Metall parallel zur Oberfläche abgetragen. |
Der gleichmäßige
Flächenabtrag der Werkstoffoberfläche wird hauptsächlich
durch chlorid- oder schwefeldioxydhaltige
Flüssigkeiten hervorgerufen. Diese Korrosionsart
wird bei un- und niedriglegierten
Stählen auch als Rosten bezeichnet.
Wenn die Abtragungsrate unter 0,1
mm/a beträgt, dann wird der Werkstoff als
ausreichend beständig gegen Korrosion
angesehen.
Auch nichtrostende
Edelstähle können rosten. Hier liegen
die Gründe darin, dass sich keine Passivschicht
bildet oder Passivschicht zerstört wurde. Deswegen
ist bei der Verarbeitung auf ein hohes Maß an Sauberkeit
zu achten und die bearbeiteten Flächen müssen
grundsätzlich von allen Rückständen gereinigt
werden. |
Rost
(x FeIIO * y Fe2IIIO3* z H2O
[x, y, z positive Verhältniszahlen])
Die Oberfläche von Eisenmetallen
(Eisen, Stahl) geht mit Sauerstoff und Wasser
bzw. Luftfeuchtigkeit eine chemische Verbindung (Oxidation) ein.
Das Produkt ist Rost (Eisenoxid [wasserhaltiges Eisenoxid]). Einige
Stoffe (z. B. Salz [Salzwasser, salzhaltiger Luft]) beschleunigen
die Rostbildung.
Rost führt dazu, dass das Material porös wird und wenn
weiter Sauerstoff und Wasser weiter vorhanden ist, die Zersetzung voranschreitet.
Das Material wird mit zunehmender Zersetzung poröser, brüchig, platzt aufgrund des grösseren
Volumens evtl. auf, bis hin zur völligen Zerstörung.
|
|
|
Zugesetzte Verteileranschlüsse |
|
|
|
Rost – Oxidation – Korrosion ist nicht das Gleiche.
Die Oxidation ist eine Elektronenabgabe eines Stoffes. Diese Elektronen müssen von
einem anderen Stoff aufgenommen werden (Reduktion). Rost ist eine spezielle Form der Oxidation.
Eine Oxidation muss nicht zu Rost führen. So entsteht z. B. bei Zink oder Aluminium durch die Reaktion mit Sauerstoff eine
hauchdünne Oxidschicht. Diese dünne Oxidschicht schützt die Metalle vor einer weiteren chemischer
Reaktion. Deswegen unterscheidet man zwischen Eisenmetallen (die rosten können) und Nicht-Eisenmetallen
(die nicht rosten). Von Korrosion (anfressen) spricht man allgemein bei einer chemischen Reaktion von Metallen mit
ihrer Umgebung, die zu einer Beeinträchtigung der Funktion bzw. Zerstörung führt.
Flugrost (Eisenstaub) ist eine beginnende Korrosion von Eisenmetallen. Gemeint ist eine
dünne Rostschicht auf einer Oberfläche, die sich leicht abputzen lässt. Flugrost kann zu einer weiteren Verrostung
führen, wenn er nicht entfernt oder die Oberfläche nicht behandelt wird.
Weißrost kann sich z .B. bei viel Feuchtigkeit auf Zinkoberflächen bilden. Wenn
die Feuchtigkeit nicht mehr vorhanden ist, breitet sich der Weißrost auch nicht mehr weiter aus. So sollten z. B. verzinkte Bleche
witterungsgeschützt (trocken) gelagert werden, weil der Korrosionsschutz gemindert wird, wenn er länger
einwirkt. |
Edelstahl gibt es in verschiedenen Arten und ist nicht mit nichtrostendem
bzw. rostfreiem Stahl gleichzusetzen, hat aber unter normalen Umweltbedingungen einen ausreichenden Korrosionsschutz,
kann aber unter bestimmten Bedingungen rosten. Das am häufigsten auftretende Problem ist die Ansammlung von
Flugrost oder der Kontakt mit rostigen Gegenständen auf einer Edelstahloberfläche.
Nichtrostenden Edelstähle mit einem Cr-Gehalt von über 10,5 %, kann die Entstehung von Rost nicht ohne weiteres ausgeschlossen werden. Selbst austenitische Edelstähle mit Cr-Gehalten von über 20 % und Ni-Gehalten von über 8 % können bei falscher Handhabung und Bearbeitung oder bei konstruktiven Mängeln rosten. |
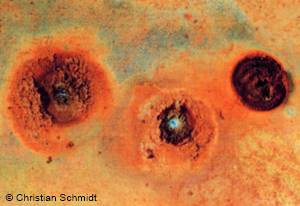 Lochkorrosion in Edelstahlleitung (Cr-Ni-Stahl 1.4401)
Korrosionsprodukte an der Rohraußenseite durch ausgetretenes Anlagenwasser in kleinster Menge
Quelle: Christian Schmidt, Versicherungskammer Bayern |
Die Lochkorrosion in Edelstahlleitungen (Bild) entstand in
einer Anlage, in der die den nach der Trinkwasserverordnung zulässigen Chloridwert überschritt. Einige Monate nach der Erstflutung der
Rohre zeigten sich am gesamten Rohrleitungsnetz aus Edelstahl (Cr-Ni-Stahl 1.4401) erhebliche Korrosionsschäden. Besonders betroffen
waren die Verbindungsstücke (Pressfittings). Die Korrosionsbeständigkeit des Edelstahls beruht auf der Bildung einer
sehr dünnen Passivschicht an seiner Oberfläche. Voraussetzung für eine Korrosion ist damit die Zerstörung dieser Passivschicht. Darüber
hinaus ist die Korrosionsbeständigkeit abhängig von der Oberfläche. Je glatter und homogener diese ist, desto
höher ist die Beständigkeit gegen korrosiven Angriff. Insbesondere durch Einschlüsse oder Ablagerungen,
z. B. eingepresste Rost- oder Staubteilchen aus der Verarbeitung, kann es zu örtlicher Korrosion kommen, die schnell um sich greift. Bei der
Lochfraßkorrosion wird die Passivschicht nur an speziellen Punkten durchbrochen. Als Folge entstehen auf der Oberfläche Grübchen oder
Löcher. Lochfraß wird im Wesentlichen durch Halogen-Ionen, vor allem Chlorid-lonen im Wasser, verursacht.
Die weitere Erhöhung des Chromgehalts, insbesondere durch Zusatz von Molybdän und zum Teil von Stickstoff, kann
die Beständigkeit der nicht rostenden Stähle gegenüber Lochkorrosion deutlich erhöhen. Die Lochfraßkorrosion von Edelstahl
sollte nicht unterschätzt werden; sie kann in Wasser- und Abwasserbereichen mit hohen Konzentrationen an Chlorid-lonen verstärkt auftreten.
|
|
|
|
Eine
Erosionskorrosion (Kavitationskorrosion
[punktuelle bzw. kleinflächige Abtragungen]) entsteht durch Kavitation
und Implosionen
an Engstellen (z. B. Rohrbögen, unentgratete Rohre, eingedrücke
verengte Rohrquerschnitte) oder in Armaturen und Pumpen in Verbindung
mit hohen Fließgeschwindigkeiten von Flüssigkeiten. Eine Erosion
kann auch durch feste Stoffe (z. B. Sand) infolge eines
Abriebes hervorgerufen werden. |
|
Quelle:
CALEFFI ARMATUREN GmbH |
|
|
|
Erosionskorrosion
oder auch Kavitationskorrosion ist eine
punktuelle bzw. kleinflächige
Abtragung eines Metalls,
die durch eine relativen hohe Fließgeschwindigkeit
an einer Metalloberfläche entsteht. Es tritt häufig
in Rohrbögen und Rohrengstellen
(Eindellungen, Verschraubungen, nicht entgratete
Schnittstellen) auf, die die Flussrichtung oder –geschwindigkeit
beeinflussen bzw. erhöhen. Der grundlegende Mechanismus
dieser Art Korrosion ist, dass ein kontinuierlicher
Flüssigkeitsstrom die schützende
Film- oder Oxidschicht von einer
Metalloberfläche entfernt. Sie kann
durch Schwebstoffe (Rost, Sand) noch vergrößert
werden. Dieser Effekt wird auch bei dem Sandstrahlen
eingesetzt, wobei selbst hartnäckige Beläge
bei relativ geringen Fliessgeschwindigkeiten
entfernt werden können. Durch die fehlende Schutzschicht
ist die Metalloberfläche ungeschützt
und wird vom korrosiven Medium (Flüssigkeiten
mit ungünstigem pH-Wert, Sauerstoff- und Elektrolytgehalten)
angegriffen und korrodiert durch die Reibung
der Flüssigkeit und den entstehenden
Mikrobläschen (Kavitation
- Implosionen), was besonders in Armaturen
und Pumpen in Heizungs-, Solar- und Kühlsystemen
vorkommen kann. |
Weiche
Metalllegierungen (z. B. Kupfer oder Aluminium)
sind besonders anfällig. Bei einer
Zunahme der Durchflussgeschwingkeit kann die thermische
Leistung, z. B. in Wärmetauschern, verbessert werden,
erhöht aber auch das Risiko der Erosionskorrosion.
Folgende Strömungsgeschwindigkeiten
sollten bei kaltem Wasser nicht überschritten
werden: |
Gusseisen
- 3,0 m/s; Edelstahl - 4,6 m/s; Kupfer - 2,4 m/s; Aluminium;
1,8 m/s |
Mit zunehmender
Temperatur erhöht sich das Risiko
der Erosionskorrosion. So gilt z. B. bei
Kupfer eine Strömungsgeschwindigkeit
von 2,4 m/s für kaltes Wasser und
darf bei 60 °C warmen Wasser 1,5 m/s
nicht überschreiten. In Wassersystemen, die ständig
über 60 °C betrieben werden, sollte die Strömungsgeschwindigkeit
nicht höher als 0,91 m/s sein. Hier
liegt auch der Grund, dass Zirkulationsleitungen
abgeglichen werden sollen. |
|
|
|
Eine
Spannungsrisskorrosion (SPRK)
entsteht durch eine Rissbildung einer inneren Spannung oder unter mechanischer
Beanspruchung in Anwesenheit von korrosionsbildenden Flüssigkeiten
(z. B. chloridhaltig und stark alkalisch) z. B. bei austenitischen CrNi-Stählen
(Edelstahl). |
|
Risse
in Armaturenexzentern; Innenoberfläche teils geschmiedet,
teils gedreht |
Quelle:
Dipl.-Ing. Wolfgang Allertshammer |
|
Eine
besondere Art der Kontaktkorrosion ist die Spannungsrisskorrosion
(SPRK), die nur dann auftritt, wenn ein Werkstück oder
Bauteil Zugspannungen enthält, der
verwendete Werkstoff eine SPRK-Empfindlichkeit besitzt und
ein spezielles Medium einwirkt. Nach Ablauf einer Einwirkzeit
bilden sich Anrisse, die nur unter mit
einem Mikroskop sichtbar sind, aus denen sichtbare Risse
entstehen, die sich senkrecht zur Richtung der
Zugspannungen ausbilden und deren Verlauf sowohl transkristallin
als auch interkristallin ist. Diese Schaden werden erst
nach einem Wanddurchbruch bemerkt. Austenitische
Chrom-Nickel-Stähle und Kupfer-Zink-Legierungen
(Messing) sind besonders anfällig. Gußwerkstoffe
gleicher Art sind widerstandsfähiger als die entsprechenden
Walz- und Schmiedewerkstoffe. |
|
|
|
|
|
Eine
Schwingungsrisskorrosion (SwRK) kann bei jedem metallische
Werkstoff in jedem Elektrolyten vorkommen. Die
Brüche entstehen ausschließlich durch
transkristalline Risse, die senkrecht zu den wirkenden Hauptnormalspannungen
entstehen. Dabei unterscheidet man zwischen einer SwRK
|
-
im aktiven
Zustand gehen die Risse
überwiegend von Korrosionsmulde an der Oberfläche aus. Dabei
treten die Risse nebeneinander auf und zeigen ein zerklüftetes
Bruchbild mit auskorrodierten Rissflanken.
-
im passiven
Zustand entstehen die Risse durch die Beschädigung
der Passivschicht aus dem Innern des Werkstoffs. Dabei entstehen glatte,
wenig verästelte Risse die keine Korrosionsprodukte bilden.
|
Die Lebensdauer
eines beanspruchten Bauteils (Zug und Druck, Umlauf-
und Wechselbiegung) ist abhängig von der Korrosionsbeständigkeit
des Werkstoffs gegenüber dem Umgebungsmedium,vom Grad seiner Aktivierung
durch Plastifizierungen, von der Höhe der mechanischen Schwingbeanspruchung
und deren Frequenz. |
|
Eine
Filiformkorrosion (fadenförmige
Korrosion) tritt bei beschichteten Metallen und Legierungen
(Stahl und Al-Legierungen) auf. Die Korrosion entsteht durch eine hohe
relative Luftfeuchte (60 bis 95 %), Verunreinigungen
der Oberfläche, ausreichende Durchlässigkeit
der Beschichtung für Wasser und Sauerstoff, Startersalze
(z.B. NaCl, Chloride [Tausalze], salzhaltige Meeresluft) und mechanische
Beschädigungen der Beschichtung. In den Küstengebieten
im westlichen Europa gibt es besonders bei Al-Legierungen im Bauwesen
(Fassadenverkleidung) Probleme. |
|
Unter der Beschichtungen
eines Metalls entstehen durch einen elektrochemischen
Vorgang fadenförmige Spuren auf dem Metall.
Hierbei übernimmt der Fadenkopf
die Rolle der aktiven Anode, dort verläuft
die Korrosion des Metalls mit gleichzeitiger Aufkonzentrierung
des Oberflächen-Elektrolyts (Feuchtigkeit). Mit
der Beteiligung von Sauerstoff verlaufen im Fadenstamm
die kathodischen Reaktionen. Angeregt
wird die Korrosion durch die Potentialdifferenz
zwischen Fadenkopf und -stamm.
Bei dieser Korrosion ist die Festigkeit
des Materials nicht gefährdet,
da die Eindringtiefe der Schädigung nicht groß
ist (< 40 um). Es handelt es sich also eher
um ein Schönheitsproblem der beschichteten
Oberfläche, die erhebliche Reparaturkosten zur
Folge haben kann. Effiziente Methoden des Schutzes sind
noch nicht bekannt.
|
|
|
Filiform-Korrosion |
|
Eine
Schwitzwasserkorrosion (Kondenswasserkorrosion)
entsteht durch Staub oder Fremdrost am niedrig- und unlegierten Stahl,
sowie an nichtrostendem CrNi-Stahl (Edelstahl). Dabei wird die Oberfläche
stark angegriffen. |
|
Die Kondenswasserkorrosion,
die sich aufgrund einer hohen Luftfeuchtigkeit
(> 60 % relativer Luftfeuchte)
mit Verunreinigungen aus der Luft
anreichert und an rauen Stellen von ungeschützten
Rohrwandungen bildet, ist die häufigste
atmosphärische Korrosion. Hierbei wirken
sich starke Temperatur- und Feuchtigkeitsschwankungen,
die zum ständigen Bilden und Abtrocknen von Schwitzwassertropfen
führen, besonders stark auf den Korrosionsfortschritt auf
der Oberfläche aus.
Die verschiedenen Verunreinigungen
in der Umgebungsluft und an der Rohroberfläche
wirken sich verschieden auf die Korrosion aus. |
|
-
Staub und Ruß
bilden sich auf der Oberfläche zu Kondensationskeime und wirken
wie ein Schwamm, der die Luftfeuchte bindet. Hier können dann
aggressive Salze aus dem Staub herausgelöst werden. Außerdem
haben Rußteilchen die Eigenschaft, auf Eisen wie eine Kathode
zu wirken, was zu einer Lokalelementbildung führt.
- Schwefeldioxid bildet Eisen(II)-sulfat
durch die Hydrolysierung von Schwefelsäure und Eisenoxid, da es
als Katalysator wirkt. Die sich bildende Schwefelsäure zerstört
den Schutzfilm auf der Oberfläche von Eisen.
- Chloride wirken wie Sulfate, sind
aber nur in unmittelbarer Meernähe und in Industriegebieten mit
säure- oder chlorverarbeiten Werken von Bedeutung.
- Stickoxide wirken wie Schwefeldioxid
und können durch die oxidierende Eigenschaft die Wirkung von Schwefeldioxid
verstärken.
- Ammoniak und Amine
wirken nur in der Nähe von landwirtschaftlichen Betrieben korrosionsfördernd,
weil sich hier Ammoniumsalze bilden. Bei Kupfer- und Aluminiumteilen
sind diese starke Korrosionsgifte, die zu einer raschen Zerstörung
des Bauteils führen können.
|
|
|
|
|
Säurekondensatkorrosion
im Kessel
|
|
Säurekondensatkorrosion
im Nachheizkasten eines Warmluft-Kachelofens |
|
Eine Taupunktkorrosion
(Säurekondensatkorrosion) entsteht
bei einer Taupunktunterschreitung, wobei Wasser oder Säure
(z. B. aus Verbrennungsgasen im Kessel oder Abgasrohr) auf
Metalloberflächen kondensieren und zu örtlichen
oder flächenhaften Schäden (gleichmäßige
Flächenkorrosion und Muldenkorrosion) führen. |
Wenn bei einer Kondensation
durch eine Taupunktunterschreitung in einem
Heizkessel Bestandteile aus dem Brennstoff
(z. B. Heizöl > Schwefel) in Lösung
gehen, dann spricht man von Säurekondensatkorrosion.
Dabei hängt die Aggressivität
des Kondensats von der Verdünnung,
der aus den schwefelhaltigen Verbrennungsgasen (konzentrierte
Schwefelsäure) ab. Stark korrosiv wirken. Aber auch
Kondensate aus chlorhaltigen Gasen (z.
B. Verbrennen chlorhaltiger Kunststoffe) wirken sehr
korrosiv. |
Die Korrosionsschäden
durch die Säurekondensat- und Taupunktkorrosion
treten in der Regel an Stellen auf, an
denen der Taupunkt unterschritten wird.
In Heizungskesseln sind diese Flächen
hauptsächlich im Bereich des Heizungsrücklaufes
und im unteren Bereich der Brennkammer bzw. Rauchgaszüge.
Aber auch im Rauch- bzw. Abgasrohr
oder im Metallschornstein kann es zur
Kondensatbildung kommen.
|
Auch
in der Rauchgasanlage eines Kachel-
oder Kaminofens, die mit schwefelhaltigen
Brennstoffen (Kohle, Braunkohlebriketts) betrieben
werden, kann es zur Durchrostung infolge jahrelanger Nichtbenutzung
bei der Verwendung von Materialien ohne Rostschutz zu Korrosionsschäden
kommen. |
|
|
|
Partikelbildung
in Kupfer-Gasleitungen |
|
|
Homogene,
schwarze, matt glänzende Schicht |
Partikel
im Gasfilter |
|
Quelle:
DBI Gas- und Umwelttechnik GmbH |
|
Partikel
im Cu-Rohr einer Solaranlage |
|
Eine Partikelbildung
an der Innenoberfläche von Kupferleitungen
in Gas-Hausinstallation (Kundenanlagen)
wird immer wieder festgestellt. Wenn sich die Partikel im Filter
an der Gasarmatur sammeln, kommt es zur Störungsmeldung,
also zum Ausfall des Gasgerätes. Der Grund
der Partikelbildung ist nicht konkret
erforscht. Es wird angenommen, dass im Schwefelgehalt
(evtl . Odormittel),
der zu einer Taupunktkorrosion
(Säurekondensatkorrosion) führen
kann, der Grund zu finden
ist. Auf der Rohrinnenoberfläche befindet
sich eine homogene, schwarze, matt glänzende Schicht
(Dicke: << 10 µm, ~2 – 3 µm), die bei
entsprechend dicker Schicht Risse bilden und abplatzen.
Folgende Partikel werden gefunden:
- Sulfide: Cu31S16 , Cu7S4
- Oxide: Cu2O
- Sonstiges: C2CuO4 •H2O
Ein Untersuchungsprogramm zur Ermittlung
des Einflusses auf die Bildung von CuS-Verbindungen
steht noch aus.
Quelle: DBI Gas- und Umwelttechnik GmbH
Solche Partikelbildung
gibt es nicht nur in Cu-Gasleitungen, sondern z. B . auch in
Solaranlagen. Hier wird immer wieder gestritten,
ob es ausgecrackte
Solarflüssigheit oder Partikel, die aufgrund
von Biofilmen
(Schwefelbildung) entstehen können, sind.
|
|
|
Odorierung |
Erdgase
und Bioerdgas (Biogas, das auf Erdgasqualität aufbereitet
wird) sind geruchsneutral. Damit Undichtigkeiten oder defekte Anlagen
schneller erkannt werden können, werden den Gasen Riechstoffe
hinzugefügt (Odorierung).
Bei der Odorierung werden organische Schwefelverbindungen
(Tetrahydrothiophen [THT]) verwendet,
die an den Geruch von faulen Eier erinnern und sehr schnell wahrgenommen
werden. Dieser Schwefelgehalt und die natürlich vorkommen Schwefelanteile
in den Gasen können besonders bei Aluminiumwärmetauscher
in Brennwertgeräten zur Korrosion führen. In
seltenen Fällen wird auch eine Partikelbildung
in Kupfer-Gasleitungen festgestellt,
die auf den Schwefelgehalt der Gase zurückgeführt wird. |
Inzwischen werden die
zentralen Orodierungsstationen auf schwefelfreie
Odorierungsmittel (Gasodor S-Free) umgestellt... Es wird schwefelfrei
auf Acrylatbasis hergestellt und erfüllt alle Anforderungen
der Deutschen Vereinigung des Gas- und Wasserfaches e.V. (DVGW) an ein
Odorierungsmittel: Es ist geruchsintensiv (wie Klebstoff oder Lösungsmittel),
ungiftig, verbrennt schadstofffrei. |
|
|
Eine
Stillstandskorrosion
(Sauerstoffkorrosion) entsteht
an unlegierten Stahlflächen in Anlagen oder Anlagenteilen, die längere
Zeit ruhendenden Flüssigkeiten ausgesetzt sind.
Hier bilden sich in sauerstoffreichen wäßrigen Medien nichtschützende,
voluminöse Korrosionsprodukte. Eine zunehmende Konzentration
kann ein Aufschaukeln der Korrosionsgeschwindigkeit
bewirken. So tritt z. B. die Lochfraßkorrosion tritt in ruhenden
Medien weitaus schneller auf als in schnell strömenden Flüssigkeiten.
Aber auch stillgelegte Maschinen (z. B. Generatoren,
Lichtmaschinen) und Geräte können diese Korrosionsart
aufweisen. Hier sind den meisten Fällen eine hohe Luftfeuchtigkeit,
verschiedene Metalle und Sauerstoffzufuhr die
Korrosionsgrundlagen. |
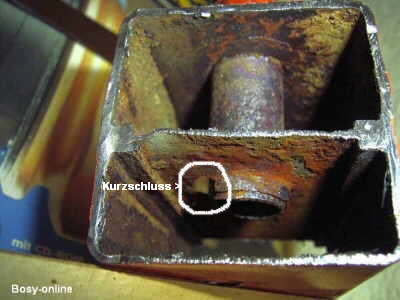
Sauerstoffkorrosion in einem Fußbodenheizungsverteiler
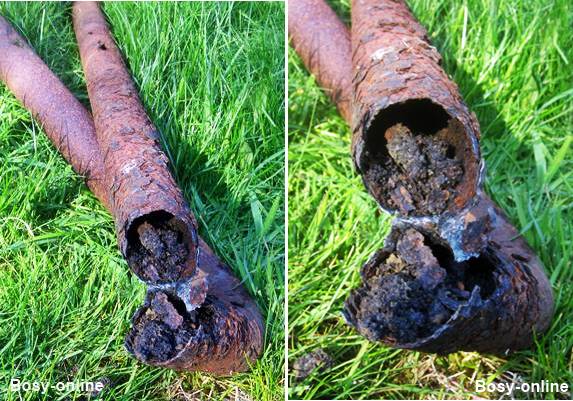
Außen- und Innenkorrosion mit Rost-
und Magnetitschlamm
|
In einem
Dampfsystem (Industrieanlagen) tritt eine
Sauerstoffkorrosion fast immer bei einem Teillastbetrieb
oder im Stillstand (Stillstandskorrosion) auf. Hier treten
elektrochemische Vorgänge auf, die
eine wässrige Lösung voraussetzen, in der Sauerstoff
gelöst ist. In trockenen, Heißdampf führenden
Leitungen, kann keine Sauerstoffkorrosion auftreten. Wird
aber nach abgestellter Dampfzufuhr der Wärmeerzeuger
(z. B. Wärmetauscher) nicht vollständig vom Kondensat
entleert, so führt infolge der Vakuumbildung zusätzlich
eindringende Luft zur Sauerstoffkorrosion.
Dabei entstehen auf dem Metall an den Berührungsflächen
Wasser-Luft (Kondensatspiegel) Korrosionsherde (mit warzenartigem
Aussehen) auf, die sich zu Narben und Löchern entwickeln.
|
Ablauf der Sauerstoffkorrosion
(Zerstörung der Magnetitschicht):
2 Fe3O4 + 1/2 O2
> 3 Fe2O3
(Eisenoxyd - rote Färbung).
|
In diesen Vorgängen
ist auch der Grund zu sehen, dass man Wassersysteme oder
vorläufig ausgebaute Teile nicht im entleerten Zustand
stehen lassen sollte.
Heizkessel
(Warmwasser, Heißwasser, Dampf) sollten grundsätzlich
erst abgeschaltet werden, wenn die Taupunkttemperatur
überschritten wurde, d. h. wenn die Brennraum- und
Abgas- bzw. Rauchgaszüge abgetrocknet
sind. Aber auch dann ist eine Taupunktkorrosion
aufgrund der schwefelhaltigen Ablagerungen
nicht ausgeschlossen.
Abgase in
den Abgasanlagen von Otto-
und Dieselmotoren, die einen Wasserdampfanteil
von mehr als 10 vol% in den Abgasen
aufweisen, sind besonders anfällig für die Stillstandskorrosion.
In betriebswarmen Abgasanlagen verhält sich dieser
Wasserdampf wie ein Gas und ist nicht korrosiv. Nach dem
Abstellen des Motors kühlt die Anlage nach kurzer
Zeit auf Umgebungstemperatur ab, der Wasserdampf kondensiert
zu Wasser und ein dünner Wasserfilm schlägt
sich auf den Innenflächen der Abgasanlage nieder.
Weitere Bestandteile im Abgas (z. B. Spuren von Schwefeldioxid)
verbinden sich dem Kondensat und beschleunigen durch ihre
aggressiven Eigenschaften den Korrosionsangriff.
|
|
|
|
Eine
mikrobiologisch induzierte Korrosion
(MIC) entsteht in Anlagen, die häufig stagnierendes
oder langsam fließendes Wasser haben. Dabei kann
das Wasser auch biozidfrei sein, weil sich Mikroorganismen,
die an den vom Wasser berührten Rohrwandungen haften, bei niedrigen
Temperaturen wachsen und vermehren. Einzelne Ansiedlungen bilden einen
primären Film bis hin zu einem makroskopischen Bewuchs (hier liegt
auch der Grund, dass Anlagen vor einer endgültigen Befüllung
gespült,
gereinigt und behandelt werden sollte). Diese Vorgänge
sind auch als "Biofouling"
bzw. auch unter den Begriff "Biokorrosion".bekannt. |
|
Wachstum
von Mikroorganismen |
|
Schäden
durch MIC |
|
Die Produkte
des Stoffwechsels der Mikroorganismen
sind die Grundlage der MIC.
Die Korrosion beruht also nicht auf der direkten Wechselwirkung
von Bakterien und/oder Pilzen mit dem Material. Der Einsatz
von "bakteriziden" Eigenschaften eines Metalls (z.
B. Kupfer und Silber) kann eine Filmbildung verhindern. |
Diese mikrobiologischen
Vorgänge können bei alle Materialien
(eingeschränkt bei Kupfer), also auch
bei Kunststoff, auftreten. Bei metallischen
Werkstoffen führt die MIC
hauptsächlich zu Flächenkorrosion, Spaltkorrosion,
Lochfraßkorrosion, Muldenkorrosion und auch Spannungsrisskorrosion.
Dort, wo die Lebens- bzw. Wachstumsbedingungen für Mikroorganismen
günstig sind (z. B. Rohrleitungen in NT-Heizungen, Kühlkreisläufe,
Kühltürme, Wasser- und Öltanks), können
erheblich Schäden auftreten. |
Im Wasser mit ansteigendem
Nährstoffgehalt (z. B. Regenwasser), ansteigender Wassertemperatur
(z. B. Trinkwasserleitungen bis ca. 30 °C) und abnehmender
oder stagnierender Fließgeschwindigkeit (Stagnationsleitungen
in der Trinkwasserinstallation) nimmt die Aktivität
der Mikroorganismen zu. Außerdem fördert
ein zunehmender Sauerstoffgehalt das Wachstum aerob aktiver
Mikroorganismen, abnehmender Sauerstoffgehalt entsprechend
das von anaerob aktiven Mikroorganismen. |
|
|
|
|
Vagabundierende
Ströme - Elektrokorrosion |
Vagabundierende
Ströme sind ein Stromfluss, der betriebsmäßig
nicht über das elektrische Leitungsnetz (L1, L2, L3, N) fließt,
aber z. B. über Rohrleitungen, Fundamenterder oder Gebäudekonstruktionen
(besonders aus FE-Metallen und Kupfer- bzw. Kupferlegierungen). Durch
diese Ströme kommt es in Verbindung mit Feuchtigkeit
der Luft oder des Bodens und mit Flüssigkeit in
Rohrleitungen (vagabundierende Ströme in Elektrolyten)
zur Korrosion. Der Schutzleiter führt
betriebsmäßig Strom. |
Die vagabundierenden
Ströme können durch Gleichstromquellen
erzeugt werden. In metallischen Leitungssystemen, erdverlegten Rohrleitungen
und Öl- und Gastanks können in kurzer Zeit Schäden
entstehen. So kann z. B. 1 mA in einem Jahr ca. 10 Gramm Fe (Eisen) zerstören.
Je höher die elektrische Leitfähigkeit
der verwendeten Flüssigkeit (Trinkwasser, Heizungswasser, Solar-
und Kühlwasser) ist, desto schneller laufen die
Korrosionsprozesse ab. Deshalb sollte hier behandeltes
VE-Füll- und Ergänzungswasser bzw. -Flüssigkeit
verwendet werden. |
Die Folge der Elektrokorrosion
kann zu Undichtigkeiten in Rohrsystemen
führen und Potenzialausgleichssysteme werden durch
korrodierte Erder gestört. |
|
|
|
Gasbildung
durch Elektrolyse |
Auch durch die Erdung
von Metallleitungen ist ein Stromfluss möglich.
Da der Schutzleiter betriebsmäßig Strom führt,
kann auch durch vagabundierende Ströme eine Gasbildung
entstehen, die zu Störungen in Flüssigkeitssystemen führen
kann. Aber auch eine "Elektrokorrosion"
ist möglich. Die Elektrolyse ist eine chemische
Reaktion, die unter Aufwand von elektrischer Energie abläuft. In
jedem Wassersystem sind verschiedene Metalle vorhanden, die in dem Elektrolyt
(Heizungswasser, besonders dann, wenn im System eine Biofilmbildung
vorhanden ist), kann es auf Grund der Unterschiede in der Spannungreihe
zu eine Stromfluss kommen. |
|
Spannungsreihe
verschiedener Metalle |
Quelle:
Rudlf Ölmann |
|
Bei der Wasserelektrolyse
handelt es sich um den Vorgang, welcher Wasser (H2O)
in Wasserstoff (H2) und Sauerstoff (O2)
spaltet. Es entsteht ein Knallgas, das eine explosionsfähige
Mischung ist. Bei dem Kontakt mit offenem Feuer (Flamme,
Glut oder Funken) erfolgt die so genannte Knallgasreaktion. |
Da dieses Gas nicht
aus der Anlage entweichen kann, bilden sich in beruhigten
Anlagenteilen (z. B. Heizkörper) Gaspolster,
die als Luftansammlungen wahrgenommen werden. |
|
Elektrolyse |
Quelle:
Planet GbR |
|
|
|
|
|
|
|
Anlaufen
/ Verzunderung
|
Eine Oxidbildung
(chemische Reaktion) wird unter dem Einfluss von
Temperatur und Gasen (Luftsauerstoff)
hervorgerufen und ist keine Korrosion sondern nur die Grundlage
für verschiedene Korrosionsarten. Bei niedrigen Temperaturen
ist die Oxidbildung gering. So entsteht z. B. bei der Erwärmen
in der Luft auf Kupfer ab ca.125 °C
eine dünne Anlaufschicht, die hauptsächlich
aus Kupfer(l)-oxid besteht. Eine Zunderung
(DIN 50 900 Teil 1 "Korrosion in Gasen bei hohen Temperaturen'')
setzt erst bei 250 °C ein. Der Verzunderungsverlust
von Kupfer besteht bei 450 °C weniger als 20 bis 40 mg/dm3
h und bei höheren Temperaturen kann eine ziemlich
starke Zunderbildung auftreten. Unter gewissen
Arbeitsbedingungen haften die Oxide fest auf dem Trägermetall
und verzögern den weiteren Angriff. Zwischen ca. 260 °C
und 1 025°C wird die rote Cu2O-Schicht
von einer schwarzen CuO-Schicht überlagert.
Oberhalb von 1025°C entsteht dann nur noch Kupfer(l)oxid. |
Der Oxidationsvorgang
(Verzunderung) bei Stahl beginnt
oberhalb von ca. 500 °C bei Wärmearbeiten
[Rohrbiegen] und Wärmebehandlung [Härten]), bei dem der
Luftsauerstoff mit dem glühenden Werkstoffbereich
zu Eisenoxid -"Zunder"- reagiert. |
Fe + O2 >
hohe Temperatur > FeO + Fe3O4 |
|
|
Korrosionsformen
und Anlagenstörungen in Flächenheizungen und Kühlsystemen |
|
Rostschlammablagerungen
verstopftes Laufrad eine Umwälzpumpe |
|
An
der Verfärbung der Rohre sieht man die ersten Magnetitablagerungen
einer neuen Anlage |
|
Allgemein treten Flächenkorrosionen
auf, die zunächst in Bezug auf die Anlagendichtigkeit
als unkritisch bezeichnet werden können. In der Praxis
kann jedoch auch ein ungleichmäßiger Flächenabtrag
stattfinden. So sind beispielsweise die für die Heizkörperherstellung
verwendeten Stahlbleche gefettet. Bei der Verarbeitung zu
Heizkörpern wird punkt- und rollnahtgeschweißt.
An diesen Stellen brennt das Fett weg, so dass diese Zonen
nicht mehr geschützt sind. Bei einer anschließenden
Berührung mit Heizungswasser wird vorhandener Sauerstoff
zunächst diese Flächen angreifen. Wenn Fettschichten
durch Berührung mit sauerstoffhaltigem Wasser nicht schnell
genug abgewaschen werden, kommt es an den nicht bedeckten
metallischen Oberflächenbereichen zu ersten Korrosionsansätzen,
die dann zu Anoden von Korrosionselementen werden. Die benachbarten
passiven Flächen bilden die Kathoden. |
Das charakteristische
Erkennungsbild für diese Korrosionsart ist das Auftreten
von örtlich begrenzten Korrosionsstellen
in einer ansonsten nicht angegriffenen Oberfläche. In
derartigen Fällen kann die korrodierte Oberfläche
mitunter nur bis zu (einhundertstel) 1/100 der Gesamtoberfläche
ausmachen. Punktkorrosion an Stahlflächen
in Fußbodenheizungsanlagen mit Kunststoffrohren sind
bislang nur vereinzelt bekannt geworden. |
Es ist jedoch denkbar,
dass unter bestimmten Voraussetzungen, wie Zusammensetzung
des Heizwassers, Fremdstoffe
und dgl. mehr, Punktkorrosionen begünstigt werden. Dem
Verfasser ist nicht bekannt, inwieweit Stahlheizkörper
und Kessel durch Punktkorrosion undicht wurden. Bei der Beurteilung
undicht gewordener Heizkreisverteiler aus Stahl ist zusätzlich
die konstruktive Gestaltung und die qualitative Ausführung
der Schweißung zu berücksichtigen. Es ist denkbar,
dass an Stellen mit mangelhafter Schweißung nur hauchdünne
Querschnitte vorhanden sind, die bei einer Dichtigkeitsprüfung
nicht festgestellt werden können. >
mehr |
|
|
|
|
|
|
Mit einem
gasförmigen Korrosionsmedium reagiert ein Werkstoff
bei der chemischen Korrosion ohne Beteiligung eines Elektrolyten
zu einem Metalloxid. Dieser Korrosionsvorgang läuft
bereits bei Raumtemperatur ab, wird aber durch hohe Temperaturen noch
beschleunigt. Es entsteht auf der Metalloberfläche eine Oxidschicht,
die z. B. vor dem Löten eines Kupferrohres entfernt werden muss.
Beim Warmbiegen von Stahlrohren entstehen Anlauffarben und es bildet sich
eine Zunderschicht, die auf chemische Korrosionsvorgänge zurückzuführen
sind. |
Auch auf der Oberfläche
von PVC-Rohren entsteht eine Oxidschicht,
die vor dem Kleben dieser Rohre ebenfalls die durch Abschälen oder
durch Auftragen von Lösemitteln entfernt werden muss. |
Auf Aluminium-
und Kupferflächen entsteht durch eine Oxidation eine gewünschte
dichte und feste Schutzschicht, die nicht durch äußere Einflüsse
zerstört werden darf, weil sonst der Werkstoff korrodiert und zerstört
wird. |
|
Hochtemperaturkorrosion
- Metal Dusting
Bei dem Metal Dusting
(MD - Metallstaub) handelt es sich um eine Art der Hochtemperaturkorrosion
(HTK) in stark aufkohlenden Atmosphären mit Kohlenstoffaktivitäten
in Verbindung mit Eisen- und Nickelbasis-Legierungen
bei Temperaturen zwischen 450 und 900 °C.
In der Heizungspraxis wirkt sich diese Korrosionsart
besonders bei der Verwendung von schwefelarmen
Heizöl bei den sog. Blaubrennern
aus. Der Schadensbereich befindert sich am Flammkopfaufsatz
und Flammrohr.
Bei der Einführung schwefelarmer Heizöle
sind an Low-Nox- und Rezirkulationsbrennern
(Blaubrenner) Schäden an Flammenrohren
aus Alloy 601 (Nickel-Chrom Legierung) nach Betriebszeiten von nur wenigen
Stunden aufgetreten. In metallographischen Untersuchungen an den geschädigten
Rohren wurde als Schadensmechanismus Metal-Dusting
(eine Art der Hochtemperaturkorrosion) identifiziert.
So schützt z. B. die MHG Heiztechnik GmbH (Raketenbrenner®)
ihre Brenner durch spezialbeschichtete Mischsysteme
und Keramik-Brennerrohre die Brenner serienmäßig
mit dem neuen Mischsystem ausgerüstet. Alle bereits installierten
Raketenbrenner® der RE 1 H-Serie können mit einem Umrüstsatz
(Keramikbrennerrohr und spezialbeschichtetes Mischsystem) nachgerüstet
werden.
Die konventionellen Stauscheibenbrenner (Gelbbrenner)
ohne NOx-Minderung und/oder Flammkopfaufsatz
sind nicht betroffen, da die notwendigen Werkstofftemperaturen
für diesen Korrosionsvorgang nicht erreicht werden. |
|
Hochtemperaturkorrosion
Der korrosive Angriff vollzieht sich in
einer Umgebung z. B. von Kohlenmonoxid
und Wasserstoff (und Wasserdampf) und Temperaturen
zwischen 450 und 900 °C vorhanden sind. In diesen reduzierenden, stark
aufkohlenden Atmosphären kommt es selbst an hochlegierten
Werkstoffen zu einer massiven Schädigung
durch Pitting (Lochfraß) oder
"Staubabtrag" aus Graphit und Metall- bzw.
Metallkarbidpartikeln, die nach Ausbruch schnell verläuft und erhebliche
Störungen an den Ölbrennern (Blaubrennern)
verursachen. |
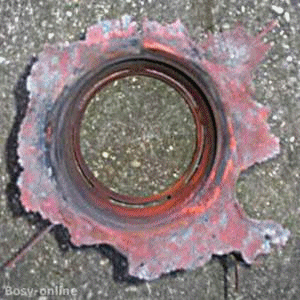
Zerstörte Flammrohre
an Blaubrennern
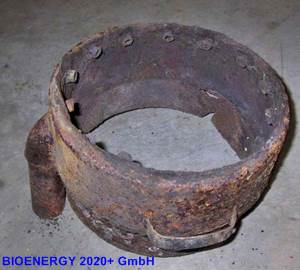
Korrodiertes Flammrohr bei
Brennstoffen mit hohem Chlor- und Alkaligehalt (z. B. für
Altholz, landwirtschaftliche und halmgutartige Brennstoffe)
Quelle: BIOENERGY 2020+
GmbH
|
Eine Hochtemperaturkorrosion
entsteht in einer Umgebung, in der neben dem
Sauerstoff und Wasserdampf auch Schwefel, Kohlenstoff, Stickstoff,
Halogene (Cl, F, I, Br) und Temperaturen zwischen
450 und 900 °C vorhanden sind.
Sauerstoff
kann in Verbindung mit Wasserdampf bei hohen
Temperaturen zu einer Beschleunigung des Oxidationsvorgangs
bei Verbrennungsvorgängen mit feuchten Brennstoffen
(z. B. Holz, Hackschnitzel, Abfälle) führen.
Kohlenstoff
führt zur Aufkohlung über die Bildung
innerer Metallkarbide im Werkstoff, dadurch entsteht
eine Verfestigung bzw. Versprödung
des Bauteil (z. B. Flammrohr). Eine extreme Art
der HTK ist das "Metal Dusting",
das bei extrem hohen Kohlenstoffgehalten in der Umgebung von Verbrennungs-
oder Vergasungsatmosphären erfolgt. Dabei kommt es zur Kohlenstoffabscheidung
(Ruß, Koks) auf der Oberfläche des Materials. Am Ende
zerfällt das metallische Bauteil
zu "Staub" aus Graphit und Metall-
bzw. Metallkarbidpartikeln.
Die Grünfäule (Green
Rot) ist auch eine Art der Aufkohlung. Hierbei
wechseln die aufkohlenden und
oxidierenden Bedingungen. Durch die Abbindung
von Chrom (Cr) wird die Bildung einer schützenden Chromoxid-Deckschicht
(CrO) verhindert und dies führt zur starken Oxidation von
Eisen-Anteilen (Fe).
Eine ähnliche
Wirkung wie Kohlenstoff hat Stickstoff. Anstatt
Metallkarbide bilden sich innere oder äußere Metallnitridphasen.
Hier reicht schon der Stickstoff in Luft aus, um bei hohen Temperaturen
eine Nitrierung der Werkstoffe
hervorzurufen.
Bei hohen Temperaturen
bilden Halogene (Cl, F, I, Br) gasförmige
Metallhalogenide. Diese Korrosionsprodukte führen
zum "Abdampfen" des Metalls,
wodurch ein sehr schneller Metallabtrag erfolgt.
Diese halogenbeeinflusste Korrosion kann bei der Verbrennung
von chlorhaltigen Biomassen (z. B. Halmgüter
[Stroh, Gras, Chinagras]) oder bei der Müllverbrennung
(z. B. PVC) auftreten.
Werkstofffragen
bei der Einführung von schwefelarmem Heizöl
Korrosion
ohne mechanische Belastung: Hochtemperaturkorrosion
Korrosionspotentials
in Biomasse-befeuerten Kesseln |
|
|
Biochemische
Korrosion (Biokorrosion) |
Die biogene
Schwefelsäure-Korrosion sind in Abwasseranlagen
seit Jahrzehnten bekannt. Da durch den stark rückläufigen Wasserverbrauch
und dem damit verbundenen Schmutzwasserabfluss wird dieses Thema immer
brisanter. Aber auch in Heizung-, Solar-,
Kühl- und Trinkwasseranlagen ist
die Biokorosion schon immer ein Problem
gewesen, nur wurde sie vernachlässigt bzw. nicht beachtet und wurde
als "gottgegeben" bzw. normal hingenommen. Hier spricht man
auch von "Biofouling".
Bei der Rohrmaterialentscheidung in Abwassersystemen
sind die Kenntnisse und Erfahrungen über Fließ- und Transportvorgänge
und über Wechselwirkungen von Abfluss und Rohrmaterial von Bedeutung.
Hier hilft nur eine regelmäßige Wartung der Kanäle und
das Beseitigen von Ablagerungen, die biologische und
biochemische Prozesse einleiten, durch Hochdruckreinigungen. |
|
Wachstum
von Mikroorganismen |
|
Die biogene Schwefelsäure-Korrosion
greift zementgebundene Werkstoffe und solche
mit Zementauskleidungen an. Notwendige
Voraussetzung für die biogene Schwefelsäurekorrosion
ist die Sulfidentwicklung. Einen entscheidenden
Einfluss haben organische Verschmutzungen
des Abwassers. Unterstützt wird die Sulfidentwicklung
durch die Abwassertemperatur, die Abflussverhältnisse
und durch Ablagerungen im Kanalnetz. |
Bakterien
sind durchaus auch in der Lage, in Heizungs-,
Trinkwasser-, Solar- und
Kühlsystemen zu existieren, denn in
jedem Wasser ist Leben. Alles Biologische in einer Anlage
wird als Bakterium bezeichnet, auch wenn es Pilze oder Algen
sein können. |
Bakterien
benötigen eine Energiequelle. Das kann Wärme
oder (was von ihnen bevorzugt wird) eine bestimmte chemische
Reaktion sein. Sie nisten sich in Unebenheiten oder Poren
ein, um dort Kolonien zu bilden. Sie bevorzugen vor allem
ölige Oberflächen, Kunststoffe und Härtebeläge.
Bakterien benötigen eine gewisse Konstanz der Lebensbedingungen,
vor allem zu Beginn der Ansiedlung. |
|
|
Sulfatreduzierende
Bakterien Das früher häufig zur Sauerstoffbindung im
Heizungs- und Kühlwasser eingesetzte Natriumsulfit verbindet sich
mit Sauerstoff zu Natriumsulfat. Da ständig mit einem gewissen Eintrag
an Sauerstoff zu rechnen ist, muss das Sauerstoffbindemittel ständig
zugesetzt werden. Das hat drei Folgen
• Die elektrische Leitfähigkeit
des Heizungswassers steigt, was den Fluss des Korrosionsstroms begünstigt |
• Die Sulfatkonzentration
steigt, was zur Bildung von Gipskristallen führen kann, wenn
Härte im Wasser vorhanden ist |
• Unter Umständen kann
das Wasser umkippen. Darunter versteht man in diesem Zusammenhang
die Bildung von Schwefelwasserstoff. Das Wasser versäuert,
stinkt und ist giftig |
Die Verursacher sind sulfatreduzierende
Bakterien, die Sulfat zu Sulfid
umwandeln. Dabei entsteht Sauerstoff, der zur Oxidation von Metallen führt.
Temperatur und Druck spielen für die Bakterien fast keine Rolle.
Aus diesem Grunde verwendet man heute nur noch dann Sulfit als Sauerstoffbindemittel,
wenn es unter ständiger Beobachtung ist. |
Eine Bakterienansiedlung
(Schichtenbildung) ist in der Lage, ihr chemisches Milieu
weitgehend selbst zu bestimmen. Auch
wenn der pH-Wert des Wassers z. B. 9
ist, kann an der Oberfläche des Metalls oder Kunststoffs ein pH-Wert
von 4,5 (Essigsäure) vorliegen.
Die In diesen gallertartigen Schichten entstehen biologischen
Prozesse, die so vielfältig sein können, dass sie praktisch
nicht zu beherrschen sind. Auch eine
Behandlung mit giftigen Chemikalien und anderen Bioziden ist in den meisten
Fällen nicht erfolgreich, weil sie nur an der Oberfläche wirken.
Die in der darunter liegenden Bakterien bilden Resistenzen
und können die durch die Mittel entstehenden Produkte aufnehmen und
verarbeiten. |
Die Legionellen
und Kolibakterien (Colibakterien) sind
nur in Trinkwasserinstallationen relevant. |
Das Colibakterium
( Escherichia coli - E. coli ) hat eine säurebildende Eigenschaft
und kommt im menschlichen und tierischen Darm vor und hat eine wichtige
Funktionen im Immunsystem. Es gibt aber auch schädliche Colibakterien
die Toxine produzieren und beim Vorliegen einer Immunschwäche Infektionen
hervorrufen können. Solche Darminfektionen sind unter dem Namen EHEC-Colitis
bekannt. |
|
|
Elektrochemische
Korrosion |
Bei der elektrochemischen
Korrosion reagieren zwei unterschiedliche Metalle bzw.
Metallverbindungen mit einer elektrisch leitenden Flüssigkeit
(Elektrolyt). In der Trinkwasserinstallation gibt es
diese Korrosionsart u. a. bei der Verarbeitung von Kupfer und verzinkten
Rohren, die in einem Kreislauf eingebunden sind (Zirkulationsleitung)
oder direkten Kontakt haben. Aber auch in Heizungs-, Solar- und Kühlsystemen
können die wechselweise angeordneten verschiedenen Metalle von Übel
sein, da es sich in diesen Anlagen immer um Kreisläufe handelt. |
Durch eine solche
Anordnung entsteht ein galvanisches Element. Hier entsteht
ein geschlossener elektrischer Stromkreis. Die Atome des unedleren Metalls
(z. B. Zink) geben Elektronen ab und gehen als positiv geladene Ionen
in Lösung. Das unedlere Metall wird dabei zersetzt. Der entstandene
Elektronenüberschuss fließt über den Leiter zum edleren
Metall (z. B. Kupfer). |
Der Potentialunterschied
zwischen den verschiedenen Metallen wird Tabellen oder Diagrammen als
elektrochemischen Spannungsreihe dargestellt. Die Metalle
sind nach ihrem elektrischen Potential (Ladungsunterschied gegenüber
Wasserstoff) geordnet. Wasserstoff hat dabei den Wert „Null“.
Je negativer das Potential eines Metalls gegenüber Wasserstoff ist,
desto unedler ist es und je positiver sein Potential ist, desto edler
ist es. |
|
. |
|
|
Facharbeit
Leistungskurs Chemie - elektrochemische Korrosion, Schutz vor Korrosion
|
|
|
|
|
Entzinnung |
Die Entzinnung
ist eine seltene Korrosionsart, die bei gegossenen
Kupfer-Zinn-Legierungen (Zinnbronzen) vorkommen
kann. Dabei geht das enthaltene Zinn in Lösung. Dieser Vorgang
wurde in heißen chloridhaltigen Flüssigkeiten und Dampf
beobachtet. Aber auch in Anlagen mit Biofouling
können diese Legierungen korrodieren. |
Diese Legierung wird auch für Bauteile
von Umwälzpumpen verwendet. |
|
|
Grünspan
wird aufgrund seiner Farbe oft mit der Patina verwechselt. |
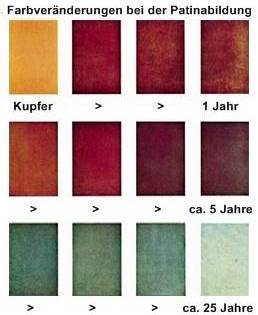
Farbveränderungen bei der
Patinabildung an der Außenluft
|
Patina
ist ein Kupfercarbonat, ein Salz
der Kohlensäure. Diese braune bis
graugrüne, aus basischen Carbonaten
und Sulfaten bestehende Oberflächenschicht
auf Kupfer und Kupferlegierungen
(Messing, Bronze) bildet sich durch die Reaktion
mit dem in der Luft enthaltenen Kohlen-
und Schwefeldioxid (und in der Meeresnähe
auch Chloriden). Die Patina wird auch
als "Edelrost" bezeichnet und Kupfer
vor der Verwitterung (Korrosion)
schützt. Teilweise wird es auch künstlich
hergestellt um Bauteile, die der Witterung ausgesetzt
sind (Dächer, Dachrinnen, Fallrohre, Fassaden, Kirchtürme,
Denkmale), zu schützen.
2 Cu + CO2
+ H2O + O2 > CuCO3
• Cu(OH)2
Braune Patina
Kupferteile (Bleche, Regenfallrohre,
Dachrinnen), die über einen längeren Zeitraum
der Außenluft ausgesetz sind, verändern
sich zuerst optisch nicht viel. Aber nach und nach tritt
eine Farbvertiefung bis braunschwarz
oder anthrazitbraun auf. Dabei bilden
sich chemisch immer dichtere und dickere Oxidschichten
und auf den Oberflächen findet durch Luftverunreinigungen
(z. B. SO2) eine langsame chemische
Umwandlung der Kupferoxidschichten
in basische Sulfate statt.
Grüne Patina
Nach einer farblichen Stagnation verändert
sich auf geneigten Dachflächen die
Schutzschicht. Es entsteht bei trockenem Wetter zunächst
ein leichter Grünschimmer auf dem
dunklen Untergrund sichtbar, die sich zunehmend durch
die ständige Einwirkung von Niederschlagwasser
und die damit verbundene verstärkte Bildung
basischer Kupferverbindungen zum kupfertypische
Patina-Grün entwickelt. Dieser Vorgang kann
8 bis 15 Jahren oder noch länger dauern.
|
|
|
|
Grünspan an einem Messingaußenteil |
|
Grünspan
Grünspan ist ein wasserlösliches Salz der
Essigsäure in Verbindung mit Kupfer oder
Messing. Es ist ein Gemisch basischer Kupfer(II)-Acetate von grüner oder
blauer Farbe, zerstört das Kupfer und ist giftig. Grünspan
entsteht aus der Reaktion von Kupfer mit Essigsäure.
In Trinkwasserleitungen ist die Bildung von Grünspan nicht möglich, weil dort keine Essigsäure vorhanden ist.
Als Kupfermineral hat Malachit auch giftige Eigenschaften.
Dort wo sich eine dichte Malachitschicht bildet, gibt es keine Probleme bei der
Stagnation des Wassers in Kupferrohren.
Grünspan entfernen
Grünspan ist nicht mit Malachit zu verwechseln!
|
|
Malachit: Cu2(OH)2CO3 (blau-grüne Kristalle)
Kupferacetat:
Cu(CH3COO) • 2Cu(OH)2 (blau bis
blaugrüner Farbton)
Neutraler Grünspan: (Cu(CH3COO)2
(bläulich-grünem Farbton)
|
|
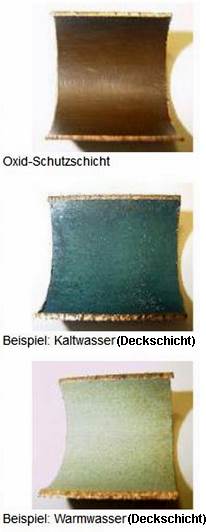
Schutz- und Deckschichten
Quelle: Deutsches Kupferinstitut e.V.
.
.
. |
Malachit
Die braune Schicht an den Wandungen in Kupferrohrleitungen in der
Trinkwasserinstallation ist eine Schutzschicht (Kupfer(I)-Oxid [Cu2O]) bzw. ein Korrosionsschutz . Diese Oxidschicht bildet sich bei der Inbetriebnahme der Anlage
aufgrund der natürlichen Reaktion des Kupfers mit dem im Wasser gelösten Sauerstoff.
Danach reagieren die Gase und Salze, die im Wasser
enthalten sind, auf der Oberfläche der Schutzschicht. Diese Deckschicht, die hauptsächlich aus
basischen Kupfercarbonaten (hauptsächlich Malachit [Cu2(OH)2
CO3) besteht. Die Farbe dieser Deckschicht in Kaltwasserleitungen kann je nach Wasserzusammensetzung
von türkisblau bis sattgrün variieren, in der Regel stellt sich eine grünliche
Färbung ein. Hierdurch wird diese erwünschte Deckschicht oftmals aus Unkenntnis
mit Grünspan verwechselt. Grünspan ist ein Salz der Essigsäure, also ein Reaktionsprodukt
aus Kupfer mit Essigsäure. Da aber in Trinkwasserleitungen kein Essig transportiert wird,
kann auch kein Grünspan entstehen. Darüber hinaus ist die Farbe der Deckschicht abhängig vom
Sauerstoffgehalt des Wassers und hat deswegehn in Warmwasserleitungen in der Regel einen
bräunlichen Farbton.
Bei Kupferrohrinstallationen ist somit die Deckschichtbildung ein natürlicher, nützlicher
und vor allem ein erwünschter Vorgang. Im Handel werden Markenrohre (z. B. SANCO, WICU, cuprotherm) angeboten, die mit
einem werkseitigen Korrosionsschutz versehen sind.
Auch bei einem neu verlegtes Kupferdach und eine Kupferfassade wechselt sich nach einiger Zeit
die Farbe in ein dunkles Rot, das durch Kupfer(I)-oxid verursacht wird. Das Kupfer reagiert dabei
mit dem Luftsauerstoff. Danach wird das Dach noch dunkler und es entsteht schwarzes Kupfer(II)-oxid. Eine
grüne Patina aus Malachit bildet erst nach
einigen Jahren durch die Einwirkung von Kohlenstoffdioxid, Luft und Wasser (2 Cu + CO2 +
H2O + O2 > CuCO3 • Cu(OH)2).
Das Kupfermineral Malachit hat auch giftige
Eigenschaften. Wasser, in dem ein Malachit gelegen hat, sollte daher niemals getrunken werden. Ebenso gefährlich ist das
Zersägen oder Zerstoßen eines Malachits ohne geeignete Schutzmaßnahmen (Staubmaske, Staubsauger), da der
feine Staub beträchtliche Mengen an löslichem Kupfer freisetzt und entsprechend giftig ist.
Malachit ist nicht mit Grünspan zu verwechseln! |
Machalitstein
Quelle: Heilsteine-Ratgeber
Polierter Machalit
Quelle: Singer-Edelsteine
.
. |
Der Malachit ist auch ein Schmuckstein,
der im Kunstgewerbe verwendet wird. Er ist ein häufig vorkommendes Mineral aus der Klasse der
Carbonate. Es kristallisiert im monoklinen Kristallsystem und entwickelt meist massige oder traubige gebänderte Aggregate,
in seltenen Fällen auch nadelige prismatische Kristalle in verschiedenen Grüntönen.
Der Malachit ist ein basisches Kupfercarbonat mit der chemischen Formel
CuCO3 • Cu(OH)2). Die Kupfer-Atome sind für die grüne Färbung verantwortlich.
Oft kommt es zusammen mit dem Mineral Azurit vor.
Das Kupfermineral Malachit auch giftige Eigenschaften. Wasser, in dem ein Malachit gelegen hat, sollte daher niemals getrunken werden. Ebenso gefährlich ist das Zersägen oder Zerstoßen eines Malachits ohne geeignete Schutzmaßnahmen (Staubmaske, Staubsauger), da der feine Staub beträchtliche Mengen an löslichem Kupfer freisetzt und entsprechend giftig ist.
Der Malachit wird auch als "Stein der Hoffnung" bezeichnet.
Die positiven Schwingungen und Energien von Edelsteinen sind Menschen bereits seit Jahrtausenden bekannt und werden aufgrund ihrer Wirkungen genutzt. Sie werden zur Heilung und Behandlung von körperlichen und psychischen Problemen und auch zur Steigerung des Wohlbefindens verwendet. Die Energie wird dabei auf verschiedene Arten übertragen, wobei der direkte Hautkontakt die häufigste Variante ist. Der dunkelgrüne Malachit ist ein sehr kräftiger Stein, dem allein und in Verbindung mit anderen Edelsteinen besondere Kräfte nachgesagt werden. Als Stein der Hoffnung hilft er dabei, die Selbsterkenntnis zu stärken und Zufriedenheit aufzubauen.
|
|
|
|
Korrosion führt
zu erheblichen Schäden an und in technischen
Geräten und Anlagen. Die DIN EN ISO 8044
unterscheidet 37 Korrosionsarten und die DIN EN ISO 12944-2
legt die Umgebungsfaktoren fest, die Korrosion beeinflussen
können. Im folgendenden sind häuftig auftretende aber auch selten
vorkommende Korrosionsarten alphabetisch aufgeführt. Einige Korrosionsarten
bzw. Korrosionserscheinungen fallen prinzipiell unter
einen Sammelbegriff, weichen aber in speziellen Errscheinungsformen voneinander
ab. |
Aktivierung
Biokorrosion - Biochemische Korrosion
Blätterteigkorrosion
chemische Korrosion
Dauerbruch
ebenmäßige Korrosion
elektrochemische Korrosion
Elektrokorrosion
Entaluminierung
Entnickelung
Entsilicierung
Entzinkung
Entzinnung
Erosionskorrosion
Explosionskorrosion
Flüssigmetallkorrosion
Gaskavitation
Graphitierung
Grünspan
Hochtemperaturkorrosion
interkristalline Korrosion
Kavitationskorrosion
Keramikkorrosion
Korngrenzenkorrosion
Korrosion
Kontaktkorrosion
Kunststoffkorrosion
Lochfraßkorrosion
Messerlinienkorrosion
Messerschnittkorrosion
mikrobiologisch induzierte Korrosion
Partikelbildung in Kupfer-Gasleitungen
Passivierung
Passungsrost
Reibkorrosion
Rost
Rougebildung
Säurekondensatkorrosion / Odorierung
Salzkorrosion
Sauerstoffkorrosion
Schichtkorrosion
Schwingungsrißkorrosion
selektive Korrosion
Spaltkorrosion
Spannungsrißkorrosion
Spongiose
Stillstandskorrosion
Streustromkorrosion
Taupunktkorrosion / Odorierung
Tropfenschlagkorrosion
Tunnelkorrosion
Wasserstoffversprödung
Wasserstoff- und Sauerstoffkorrosion
Weißrost |
|
|
|
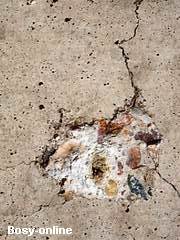
Beton mit Alkali-Kieselsäuregel
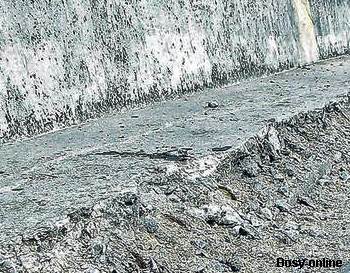
Schäden an einer Brücke
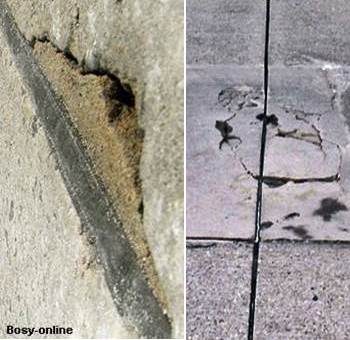
Straßenschäden
|
Betonkrebs
ist die umgangssprachliche Bezeichnung für eine Alkali-Kieselsäure-Reaktion
(AKR). Hier reagieren alkaliempfindliche SiO2-Bestandteile
der Gesteinskörnung mit den Alkali- und Hydroxid-Ionen (K+,
Na+ und OH-) der Porenlösung im Beton zu einem Alkali-Kieselsäuregel.
Dieses Gel ist bestrebt, Wasser aufzunehmen.
Dadurch vergrößert sich das Volumen mit der Zeit so
stark, dass lokal Quelldrücke auftreten,
die das Betongefüge schädigen und äußerlich
zu Netzrissbildung, Ausblühungen und Abplatzungen führen
können. Die ersten sichtbaren Schäden
treten flächig und/oder an den Rändern
der Betonbauteile (z. B. Betonwände, Dehnungsfugen
im Straßenbelag, Ränder an Straßenbrücken)
auf .
Die AKS tritt besonders dann stark auf, wenn zur Betonherstellung
Gesteinskörnungen verwendet werden, die
reaktionsfähiges Siliziumdioxid enthalten
und dieses mit den Alkalien im Beton reagiert.
Eine Alkali-Kieselsäure-Reaktion kann in vielen
Betonen ohne eine Schädigung des Betons ablaufen und ohne
die Stand- bzw. Verkehrssicherheit und die Dauerhaftigkeit zu
beeinträchtigen.
Normalerweise treten erst nach 5
bis 15 Jahren Schadensbilder
auf. Hier wird dann die Dauerhaftigkeit des Betons
beeinträchtigt, aber die Standsicherheit
der betroffener Bauteile ist jedoch in der Regel nicht
gefährdet.
Voraussetzungen für einen
Betonkrebs sind:
·
ausreichende Feuchtigkeit
· alkaliempfindliche
Gesteinskörnung (siliziumdioxidhaltige
Gesteinskörnungen)
·
hoher wirksamer Alkaligehalt in der Porenlösung des Betons
Der Betonkrebs wird
nur an Betonteile festgestellt, die mit Wasser
und Bodenfeuchte in Kontakt kommen. Dabei handelt
es sich hauptsächlich um Betonfahrbahnen, Straßenbegrenzungen,
Betonbrücken, Staudämmen, Tunnel und Eisenbahnschwellen.
Ein Betonkrebs kann durch zwei Maßnahmen
vermieden werden:
·
Austausch der alkaliempfindlichen
Gesteinskörnung
·
Reduzierung des Alkaligehaltes der
Porenlösung des Betons
Schadhafte Bauteile
oder Straßenbelege können nur durch
eine Erneuerung des gesamten Bauteils bzw. Belages
saniert werden.
Alkali-Kieselsäure-Reaktion
im Überblick - VDZ |
|
|
|
Um Metalle vor
Korrosion zu schützen gibt es verschiedene
Maßnahmen (s. Tabelle). Die Maßnahmen beginnen bei
der Fertigung der Werkstoffe über die Lagerung
des Materials und der Planung der Anlage und enden mit
bzw. nach dem richtigen Einbau. In den meisten Fällen
reicht eine einzelne Maßnahme nicht aus, um einen vollständigen
Schutz zu bieten. Die DIN EN ISO 8044 unterscheidet 37 Korrosionsarten
und die DIN EN ISO 12944-2 legt die Umgebungsfaktoren fest,
die Korrosion beeinflussen können. |
Korrosionsschutzmaßnahmen |
|
oberflächentechnische
Maßnahmen
|
werkstofftechnische
Maßnahmen
|
elektrochemische
Maßnahmen
|
|
|
|
Fließrichtung
des Elektrolyts (Fließregel) |
Kathode/Anode |
metallische
Überzüge |
Legierungselemente
(Cr, Ni, Mo, Cd)
|
Leitfähigkeit
der Elektrolyten herabsetzen (Inhibitoren) |
kathodischer
Schutz ohne Außenstrom |
Druckentspannung |
Stabilisatoren bei Austeniten
(Ti, Nb, Ta)
|
Elektrolyt -
Zusammensetzung und Temperatur |
Werkstoffpaarungen
mit geringer Potentialdifferenz |
Glätten
der Oberflächen |
Wärmebehandlungen,
wie Spannungsarmglühen, Lösungsglühen, Diffusionsglühen,
Abschrecken von Austenit |
Sauerstoffkonzentration
des Elektrolyts (Belüftung) |
Vermeidung von
Verunreinigungen und Spalten |
Entfernen von
Anlauffarben |
|
|
In der Praxis wird man in Heizungs-,
Solar- und Kühlsystemen immer nur
Mischinstallationen vorfinden. Der Einsatz von korrosionsbeständigen
Werkstoffen in allen Bereichen einer Anlage ist meistens nicht
möglich, wobei auch häufig der Materialpreis
und das fehlende Fachwissen eine Rolle spielt. Eine fachgerechte
Spülung,
Reinigung und der Einsatz von VE-Wasser
mit korrosionshemmenden Heizwasserzusätzen
((Inhibitoren, Frostschutzmittel)) ist eine Grundlage, den meisten Korrosionsarten
keine Chance zu geben. |
|
|
Kathodischer
Korrosionsschutz |
Man unterscheidet zwei
Schutzverfahren: |
-
Galvanischen Anoden.
Diese Magnesium-Schutzanoden (-Opferanoden)
besitzen eine grosse Differenz in der elektrochemischen Spannungsreihe
bezogen auf das Schutzobjekt (z. B. Bei Stahl <> Magnesium 2,31
Volt). Die Wassererwärmer werden in Verbindung mit der eingesetzten
Anode nach DIN 4753 Teil 6 (und DIN EN 12828) auf
die Wirksamkeit überprüft und zertifiziert. Deshalb dürfen
beim Auswechseln immer nur die gleichen Anoden
eingesetzt werden. Galvanische Anoden sind löslich und werden
aufgebraucht. Man muss sie regelmäßig kontrollieren und
evtl. reinigen oder wechseln.
-
Fremdstromanoden.
Hier werden hauptsächlich unlösliche Titan-Mischoxyd-Anoden
eingesetzt, die isoliert in den Behälter eingebaut werden. Ein
Potentiostat versorgt die Anode mit Fremdstrom. Unlösliche Fremdstromanoden
sind grundsätzlich wartungsfrei.
|
|
|
Isolierverschraubung
(galvanisches Trennstück) |
Der Einbau einer Buntmetallarmatur
(Rotguss, Messing) soll nach der DIN 1988-7 angeblich
ausreichen, um Rohrwerkstoffe unterschiedlicher
Potenziale, z.B. verzinkter Stahl und Edelstahl, vor elektrochemischer
Korrosion zu schützen. Aber schon bei Flüssigkeiten
mit hoher elektrischer Leitfähigkeit (Elektrolyt)
und bei Trinkwasser mit Härtegraden >15 °dH,
die eine vermehrte Inkrustation erzeugen, ergibt sich
ein Korrosionsrisiko. Durch den Einsatz einer Isolierverschraubung
kann die Korrosion nicht stattfinden, da die metallischen Kontaktflächen
gegenseitig isoliert sind, weil sie aus gleichartigem Material bestehen. |
|
Kyburz
® Isolierverschraubung |
Quelle:
INRAG AG |
|
|
Bauteile
einer Isolierverschraubung |
Quelle:
Viega GmbH & Co. KG |
|
Wenn der Speicher
oder Wärmetauscher und die Rohrleitungen
aus verschiedene Werkstoffen bestehen und
sich berühren, kann es zu Kontaktkorrosion
kommen. Durch die Verwendung eines Isolierschraubteiles wird
die Kontaktkorrosion durch die isolierende Kunststoffschicht
und die Anschlüsse aus zu Rohrleitung und Speicher passenden
Werkstoffen verhindert. Außerdem wird z. B. der TW-Speicher
vor vagabundierenden Strömen geschützt
und ein vorzeitigem Abbau der Opferanode wird verhindert.
Das Isolierschraubteil trennt die Leitung elektrisch auf und
verhindert auf diese Weise einen schädlichen Stromfluss.
In diesen Fällen darf der TW- Erwärmer selbst nicht
in den Potenzialausgleich mit einbezogen
werden. |
Die Isolierverschraubung
besteht aus einem Gehäuse und einer
Hülse. Die Hülse ist durch eine
isolierende Kunststoffschicht stabil und
unlösbar mit dem Gehäuse verbunden und mit Ihrem
Innengewinde an den Speicher oder Wärmetauscher montiert.
Die Rohrleitung wird dann mittels Einlegeteil und Überwurfmutter
an das Aussengewinde des Isolierschraubteils geschraubt. |
|
|
|
Durch eine unzulässige
Mischinstallation (Galvanische Spannungsreihe)
bzw. durch Fehlströme (nicht geerdete
Anschlussleitungen, kein Potentialausgleich) treten bei
einer Kontaktkorrosion treten bei den
Anschlüssen starke Korrosionsschäden
auf. |
Ist eine Mischinstallation
nicht zu vermeiden, so sind in jedem Fall, in Fließrichtung
gesehen, das edlere nach unedleren
Werkstoffen einzusetzen. Welches Metall
edler ist, ergibt sich aus der elektrochemischen
Spannungsreihe. eingesetzt. Bei den wichtigsten
Metalle ergibt sich folgender Verlauf: |
Magnesium (Mg)
– Aluminium (Al) – Zink (Zn) – Chrom
(Cr) – Eisen (Fe) – Zinn (Sn) – Blei
(Pb) – Kupfer (Cu) – Gold (Au) |
Je weiter zwei
Elemente in der Spannungsreihe auseinander sind, umso
schneller wird das undedlere Material verbraucht. Durch
Isolierverschraubungen ist eine elektrische
Trennung herzustellen. |
|
|
Korrosion
an Speicheranschlüssen |
Quelle:
Austria Email AG |
|
|
|
Quelle:
Viega GmbH & Co. KG |
Wenn
bei einer Reparatur ein Teilstück einer Rohrleitung
mit anderem Material mit Isolierverschraubungen ausgetauscht wird,
dann müssen die Teile, die untereinander elektrisch leitfähig
verbunden waren, nach VDE 0100 mit einem Potenzialausgleich
mit einem Erdungsleiter NYM-J 1 x 6 mm2 zu verbinden. |
|
|
Isolierverschraubung
für Heizöl - doppelt und einfach isoliert |
Quelle:
INRAG AG |
Die Isolierverschraubung
trennt Kupferleitungen in Heizölleitungen
elektrisch auf. Sie unterbindet Ströme und daraus resultierende
Magnetfelder. Sie wird bei Tankanschlüssen
für Heizöl eingesetzt und trennt Spannungen bis 1500 Volt
(VSM) respektive 3000 Volt (VDS). |
|
|
|
|
Mit einer Analyse
wird die Heizungswasserqualität festgestellt. Die
Probennahme und die Analyse sollte grundsätzlich
von einem Fachunternehmen, das die theoretischen und
praktischen Kenntnisse nachweisen kann, durchgeführt werden. Inwieweit
eine Analyse per Internet durchgeführt werden kann, muss jeder für
sich entscheiden. > mehr |
|
|
|
Beschichtungen
werden zum Schutz von Metallen gegen
Korrosion eingesetzt. Die DIN EN ISO 12944 befasst sich
mit dem Korrosionsschutz von Stahlbauten durch Beschichtungssysteme.
Beschichtungen werden dem passiven Korrosionsschutz
zugeordnet und umfassen alle Maßnahmen, die Oberflächen gegen
korrosive Medien abschirmen. > mehr |
|
|
Eine korrosive
Zersetzung der metallischen Komponenten (Rohre,
Fittings) von Rohrleitungen durch äußere
Feuchteeinwirkung war und ist bei der Außenkorrosion
im Erdreich und Feuchträumen allgemein bekannt. In den letzten
Jahren treten diese Korrosionen auch verstärkt
bei Rohrleitungen in Gebäuden auf. Gutachter haben
diese Rohrbruchschäden in Rohrleitungen mit den
neuen Pressfittingsysteme mit Metallrohren
und Mehrschichtverbundrohren festgestellt. >
mehr
|
|
ich
arbeite dran |
|
|
|
|
Videos
aus der SHK-Branche |
SHK-Lexikon |
|
|
|
Hinweis!
Schutzrechtsverletzung: Falls Sie meinen,
dass von meiner Website aus Ihre Schutzrechte verletzt werden, bitte ich
Sie, zur Vermeidung eines unnötigen Rechtsstreites, mich
umgehend bereits im Vorfeld zu kontaktieren, damit zügig
Abhilfe geschaffen werden kann. Bitte nehmen Sie zur Kenntnis: Das zeitaufwändigere
Einschalten eines Anwaltes zur Erstellung einer für den Diensteanbieter
kostenpflichtigen Abmahnung entspricht nicht dessen wirklichen oder mutmaßlichen
Willen. Die Kostennote einer anwaltlichen
Abmahnung ohne vorhergehende Kontaktaufnahme mit mir wird daher im Sinne
der Schadensminderungspflicht als unbegründet zurückgewiesen. |